С. А. Горлов – ООО «КомАп Системс»
Проект перевода дизельного энергетического комплекса в двухтопливный режим работы с помощью системы производства ComAp реализован для ОАО «Томскнефть» ВНК. Генподрядчиком модернизации выступала компания ООО «А.Д.Д. Сервис» совместно с генпроектировщиком НИПИ «Сибпроект-Сервис».
В апреле 2009 года был введен в эксплуатацию энергетический комплекс, оборудованный системой двухтопливного режима работы HSC 1100 (далее СДТР) производства чешской компании ComAp. Энергокомплекс входит в систему электроснабжения Тагайского нефтяного месторождения, расположенного в Томской области, и состоит из трех комплектных дизельных электростанций контейнерного исполнения.
ДЭС выполнены на базе дизель-генераторных установок Р800 Р1 производства FG Wilson с двигателями Perkins 4006-23TAG. Для энергокомплекса предусмотрен следующий режим работы: две ДЭС постоянно работают параллельно на общую силовую шину, одна – находится в резерве. Передача электрической мощности потребителям производится по воздушной линии напряжением 6,3 кВ. Общая потребляемая электрическая мощность составляет 600 кВт – она равномерно распределяется между работающими ДЭС. В случае аварийного останова одной из них, общую нагрузку принимает работающая станция до момента пуска и синхронизации резервной ДЭС.
Основная цель модернизации энергокомплекса на двухтопливный режим – это использование попутного нефтяного газа (далее ПНГ) в качестве топлива для производства электрической энергии. Это позволяет не только существенно снизить расходы на дизельное топливо, но и утилизировать соответствующий объем ПНГ.
До начала модернизации на месторождении уже существовала инфраструктура, связанная с первичной подготовкой газа, поэтому оставалось подвести газ непосредственно к энергокомплексу и установить газораспределительный пункт (ГРП). Он обеспечивает снижение давления магистрального газа до уровня входного давления газовых магистралей двигателей и распределение газа между ними. ГРП представляет собой систему трубопроводов с соответствующей запорной газовой арматурой, обходной (байпасной) линией, фильтром очистки газа, устройствами, обеспечивающими регулирование и контроль давления газа, безопасную эксплуатацию оборудования.
Работы были разбиты на два этапа: монтаж оборудования и пусконаладка. Первый этап включал в себя сборку и монтаж в отдельном контейнере ГРП, размещение в контейнерах ДЭС панелей управления СДТР, установку газовых магистралей. Во впускном тракте дизельных двигателей были установлены газовые смесители, датчики детонации и измерения температур, датчики положения распределительных валов двигателей; проложены кабели управления и измерений, смонтирована защитная арматура.
Газ из магистральной линии заказчика по трубопроводу поступает на вход ГРП, его максимальное давление здесь составляет 0,4 МПа, расход – 300 м3/ч. Затем газ проходит через осевой компенсатор, входной запорный шаровой кран и подается в газовый фильтр. Между осевым компенсатором и запорным краном установлен манометр для измерения давления газа на входе в газораспределительный пункт. Проходя через фильтр, газ очищается от твердых примесей и через клапан безопасности поступает в регулятор давления. Здесь давление газа снижается до 0,033 МПа – значения, необходимого для нормальной работы газовой магистрали двигателя. Для измерения давления газа на выходе из ГРП на выходе регулятора установлен манометр.
После регулятора давления газ проходит через выходной запорный шаровой кран и по трубопроводам подается на газовые магистрали двигателей. ГРП имеет обводную (байпасную) газовую линию с запорным шаровым краном и газовой заслонкой. Обводная линия предназначена для подачи газа в газовые магистрали двигателей во время проведения работ по техническому обслуживанию ГРП.
Максимальное давление газа на входе газовой магистрали – 0,035 МПа. Через запорный шаровой кран газ подается в газовый мультиблок. В состав этого устройства включены два отсечных электромагнитных клапана, датчики входного и выходного давления газа и регулятор давления. Датчик входного давления выдает сигнал на закрытие отсечных электромагнитных клапанов мультиблока при давлении ниже 0,015 МПа, датчик выходного давления – на закрытие при давлении выше 0,005 МПа. В обоих случаях подача газа в двигатель прекращается.
С помощью регулятора давления поддерживается постоянный перепад давления газа и воздуха во впускном патрубке двигателя. Для измерения давления газа на выходе мультиблока предусмотрен манометр. Дозирование необходимого количества газа производится с помощью газового актуатора. Через разветвитель с шаровыми кранами по гибким шлангам газ поступает к двум газовым смесителям, установленным на впускных патрубках турбонагнетателей двигателя.
В случае сокращения подачи газа в общую магистраль, газовые клапаны автоматически перекрываются, и двигатель продолжает работу только на дизельном топливе. Переход происходит мгновенно, без скачков выходной мощности. При возобновлении газоснабжения двигатель автоматически переходит на двухтопливный режим работы.
После завершения первого этапа работ по монтажу оборудования компания «Томскнефть» выполнила работы по установке системы подготовки попутного газа для его использования в качестве топлива и подвод газа к ГРП и ДЭС. Система подготовки состоит из сетчатого сепаратора, общего для всего энергокомплекса, а также сепараторов, установленных на каждой генераторной установке. Кроме того, на входе в газораспределительный пункт предусмотрены фильтрующие элементы.
Второй этап включал в себя тестирование работы двигателей на дизельном топливе при различных нагрузках, проверку установки всего комплекса оборудования, конфигураций управляющих контроллеров, настройку газового оборудования ГРП и газовых магистралей двигателей. Затем были проведены пусконаладочные работы и приемосдаточные испытания энергокомплекса.
В ходе пусконаладочных работ определялись оптимальные настройки системы управления газового оборудования ГРП и газовых магистралей двигателей, которые обеспечивали стабильную работу дизель-генераторных установок в автономном и параллельном режимах на различных нагрузках при замещении дизельного топлива газовым (табл.).
В итоге двухтопливная система обеспечила стабильное замещение дизельного топлива газовым на уровне 45 % при рабочей нагрузке ДГУ около 300 кВт. Данный процент замещения является оптимальным при таких условиях, причем следует отметить, что с увеличением нагрузки этот показатель можно увеличить при сохранении стабильной работы ДГУ в пределах нормальных эксплуатационных параметров.
Система управления обеспечивает контроль, автоматическое управление и регулирование всей СДТР. Двигатель запускается на дизельном топливе, нагружается и плавно переводится в двухтопливный режим. Датчики контроля детонации устанавливаются на головках цилиндров двигателя. С их помощью система управления обнаруживает моменты взрывообразного сгорания топлива (детонацию), крайне опасные для двигателя.
Детонация устраняется путем автоматического изменения соотношения дизельного и газового топлива. Кроме того, система управления определяет положение распределительного вала двигателя, частоту вращения коленчатого вала, температуру наддувочного воздуха и выхлопных газов двигателя. Эти параметры непосредственно влияют на протекание двухтопливного процесса.
Система управления осуществляет функции мониторинга параметров, защиты и оповещения при возникновении аварийных ситуаций.
В автоматическом режиме САУ самостоятельно начинает подачу газа в двигатель и регулирует его количество в соответствии с текущей нагрузкой. При снижении нагрузки до минимального уровня подача прекращается. Система мониторинга с помощью ПК и специального программного обеспечения позволяет удаленно управлять двухтопливным процессом и контролировать основные его параметры по всем генераторным установкам, входящим в энергокомплекс, получать сообщения об аварийных ситуациях и сохранять историю событий.
В состав САУ входит панель управления, набор датчиков и комплект электрических кабелей. Панель управления представляет собой электротехнический металлический шкаф, на передней стенке которого установлены: управляющий контроллер InteliGen-BF, выключатель электропитания, сигнальные лампы и кнопки управления. На нижней стенке имеются вводы для подключения электрических кабелей. Внутри панели расположены модуль расширения IS-AIN8, элементы электрозащиты, клеммные колодки и т.д.
Программное обеспечение WinEdit базируется на Windows 2000/XP/Vista и обеспечивает следующие основные функции:
• оперативный мониторинг контроллера или группы контроллеров в пределах группы генераторных установок с отображением однолинейной схемы;
• просмотр всех измеряемых и вычисляемых значений;
• просмотр записей журнала событий контроллеров;
• настройка параметров системы.
Связь с пунктом контроля осуществляется по кабельной линии (протокол RS232). Информация, получаемая системой управления от датчиков, позволяет непрерывно контролировать протекание двухтопливного процесса и обеспечивать необходимую защиту двигателя.
Приемосдаточные испытания энергокомплекса проводились с имитацией различных режимов работы генераторных установок, в том числе и аварийных. Двухтопливная система продемонстрировала устойчивую работу во всем диапазоне мощности. Она была проверена также и в условиях ступенчатого изменения нагрузки (последовательные сбросы/набросы). При имитации аварийных ситуаций (например, внезапное отключение по причине аварии одной из двух параллельно работающих генераторных установок) система адекватно реагировала на ситуацию и обеспечивала двухтопливный режим остающихся в работе ДГУ.
В процессе пусконаладочных работ и приемосдаточных испытаний проводился периодический контроль состояния фильтрующих элементов ГРП и газовых магистралей двигателей с целью определения качества подготовки попутного газа. При удовлетворительном качестве топливного газа СДТР обеспечивала стабильную работу в двухтопливном режиме.
Следует отметить следующее: после модернизации оборудования, как было заявлено, все характеристики энергоблоков не изменились. При этом номинальная мощность двигателей не снизилась, и все параметры (температура выхлопа, охлаждающей жидкости и т.д.), а также динамика нагружения, сохранились в пределах, заявленных производителем двигателя. Эксплуатация не усложнилась, подход остался как для дизельного двигателя.
В течении года эксплуатации общее среднегодовое замещение, с учетом сезонных и нагрузочных факторов, составило ~44,7 %, таким образом, модернизация оборудования позволила сэкономить за год около 620 тыс. литров дизтоплива и утилизировать 880 тыс. м3 попутного нефтяного газа на месторождении. 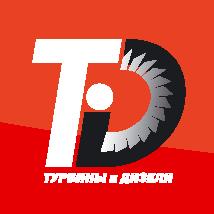