Квирийн Эппинга, Йос П. Ван Буийтенен – компания Triogen B.V.
В последние годы интерес к утилизации остаточной тепловой энергии различных технологических процессов значительно вырос. Наиболее очевидный вариант ее использования – на нужды центрального отопления. Однако при этом потребители утилизированной тепловой энергии должны находиться в непосредственной близости к месту выработки энергии. Более того, остаточное тепло может иметь более высокую температуру, чем требуется для систем центрального отопления, и в этом случае значительное количество избыточной энергии теряется. Очень часто потребности в тепловой энергии ограничены.
Преобразуя остаточную тепловую энергию в электрическую, можно передавать ее потребителям на достаточно большие расстояния. Кроме того, появляется возможность отказаться от приобретения электроэнергии из сети, что обеспечивает дополнительную прибыль. Уровни выбросов СО2 и других вредных веществ практически равны нулю. Учитывая все сказанное, были предприняты попытки создать установку, которая будет утилизировать остаточное тепло и вырабатывать электроэнергию. При этом использовались принципы органического цикла Ренкина (ORC).
В статье представлены результаты создания и применения систем данного типа компании Triogen B.V. (Нидерланды). Оборудование начали разрабатывать в 1990-х годах в технологическом университете Лапеенранта (Финляндия). Доводочные и полевые испытания установки проводились компанией Triogen B.V. с 2002 г., на рынок она была представлена в 2006 г. В настоящее время в эксплуатации находится 36 установок Triogen ORC и 10 установок готовятся к запуску в коммерческую эксплуатацию.
Конструкция установки Triogen ORC
За прошедшие годы было предпринято много попыток создать экономически выгодную установку, инвестиции в которую окупились бы за приемлемый период. Многие попытки потерпели фиаско в связи с низкими ценами на электроэнергию и отсутствие необходимых технологий и материалов – в результате за установками ORC закрепилась репутация очень дорогостоящих. Чтобы опровергнуть данное мнение, необходимо было создать оборудование с высоким КПД и низкими капитальными затратами при его установке и вводе в эксплуатацию. При этом требуемая температура цикла ORC становилась определяющим фактором: во-первых, для достижения высокой эффективности в цикле Карно и, во-вторых, для сокращения необходимой поверхности передачи энергии остаточного тепла рабочему телу в системе.
Все это было учтено при разработке установки Triogen ORC. На начальном этапе она предназначалась для утилизации тепла выхлопных газов двигателей внутреннего сгорания и турбин. Здесь температура выхлопных газов была недостаточной для выработки требуемого количества пара для привода паровой турбины, но оптимальной для обеспечения высокого КПД цикла Карно.
Для наиболее полного использования выхлопных газов необходимо было разработать химически стабильное рабочее тело с критической температурой, соответствующей минимальной температуре теплоносителя. Долгое время оптимальным для этой цели считался фреон 114, пока он не был запрещен в связи с ущербом, наносимым озоновому слою. Достойной альтернативой фреону стал толуол, поскольку он химически стабилен при максимальной температуре теплоносителя. Кроме того, его термодинамическая диаграмма оптимальна для разработки различных циклов ORC. С учетом всего этого решено было создать установку, утилизирующую сбросное тепло выхлопных газов двигателя, мощностью от 150 кВт. Такой диапазон мощности позволял использовать ее с установками, работающими на биогазе и газе мусорных свалок, а также в составе электростанций когенерационного цикла. Данные термодинамического анализа были оптимизированы для традиционного цикла ORC с рекуператором с целью получения максимальной мощности. Температура в конденсаторе сохранялась на уровне температуры окружающего воздуха. На рис. 1 представлена схема цикла и динамика процесса на диаграмме T-s. Жидкость подается из емкости для хранения на основной насос, который установлен на том же валу, что и турбина, и высокооборотный генератор. Здесь достигается высокое давление рабочего тела, при котором оно подается в рекуператор, а затем в испаритель. Сбросное тепло направляется в испаритель, в котором рабочее тело нагревается до точки кипения, испаряется и слегка перегревается. Хотя в перегреве рабочего тела нет особой необходимости, но для поддержания оптимального рабочего процесса требуется определенное количество теплоты, поскольку необходимо компенсировать потери между испарителем и турбиной.
В турбине рабочее тело расширяется, приводя ее в действие и передавая мощность на высокооборотный генератор и основной насос. После расширения определенное количество тепла рабочего тела используется в рекуператоре для предварительного подогрева жидкости перед подачей в испаритель. За рекуператором расположен конденсатор, где пар конденсируется, и затем конденсат направляется в накопительную емкость. В табл. приведены основные термодинамические данные, которые могут изменяться в зависимости от параметров источника остаточного тепла.
Конструкция основных компонентов
Высокооборотный турбогенератор
Наиболее примечательным в конфигурации цикла является расположение турбины, генератора и основного насоса на одном валу, что обеспечивает полную герметичность рабочей зоны установки. При этом в конструкции полностью отсутствуют внешние соединения с валом, поэтому не требуется внешних уплотнений вала. Смазка подшипников вала осуществляется с помощью рабочего тела в его жидкой фазе. Генератор охлаждается также рабочим телом в жидком и газообразном состоянии.
Такая особенность конструкции стала возможной при использовании высокооборотного генератора, частота вращения которого совпадает с частотой турбины. При этом устраняется необходимость в наличии редуктора, что обеспечивает высокий КПД. В составе установки используется одноступенчатая радиальная турбина. Основной насос также имеет очень простую конструкцию. Еще одним преимуществом размещения компонентов на одном валу является возможность контроля вырабатываемой мощности.
Использование рабочего тела в качестве охлаждающей жидкости для генератора и смазки подшипников обеспечивает присутствие только рабочего тела в рабочей зоне установки. Необходимость применения отдельных систем смазки и охлаждения, а также разделение смазочной, охлаждающей и рабочей жидкостей внутри установки при этом отсутствует. Исключена также возможность утечек и смешивания жидкостей. Все внешние разъемы корпуса турбогенератора фиксируются фланцевыми соединениями, обеспечивающими их полную герметичность.
Силовой вал установки имеет частоту вращения 28000 об/мин, но для достижения оптимальных эксплуатационных характеристик данный параметр поддерживается на уровне 25000 об/мин. Гидродинамические подшипники – упорные, с самоустанавливающимися сегментами – подтвердили свою надежность в процессе эксплуатации. Силовой вал расположен вертикально. Сверху установлен основной насос, снизу – турбина, из которой отработанные газы направляются вниз в рекуператор/конденсатор, а затем в виде жидкости в накопительную емкость.
Для подсоединения высокооборотного турбогенератора к статическим компонентам системы используются простые фланцевые соединения и гибкие шланги. Это обеспечивает быструю замену блока турбогенератора для технического обслуживания или ремонта. На фото 1 представлены основные компоненты установки.
Испаритель
Испаритель имеет простую гладкотрубную конструкцию, трубки малого диаметра выполнены из нержавеющей стали. Конструкция испарителя обеспечивает легкий доступ для обслуживания и очистки. Предел допустимых температур выше максимальной температуры теплоносителя, таким образом, обеспечена его высокая надежность в эксплуатации. Стандартная конструкция испарителя может быть адаптирована под специфические условия применения, такие как температура теплоносителя и величина потока.
Выхлопные газы проходят через испаритель вертикально сверху вниз. Самая низкая температура достигается в нижней точке, где собирается максимальное количество конденсата. Рабочее тело проходит по трубкам снизу вверх в прямоточном режиме.
Рекуператор и конденсатор
Функция рекуператора заключается в использовании теплового потенциала рабочего тела после расширения. Система разработана таким образом, что температура жидкости при подаче в испаритель достаточно высокая, чтобы не вызвать конденсацию выхлопных газов. Это необходимо потому, что в большинстве случаев выхлопные газы не всегда очищены от серы.
И рекуператор, и конденсатор имеют очень компактную конструкцию. Они поставляются в виде единого модуля вместе с емкостью для хранения рабочего тела, оснащенной индикатором уровня жидкости. Состояние жидкости в конденсаторе постоянно контролируется на содержание неконденсирующихся газов.
Избыточное тепло поглощается охлаждающей жидкостью (вода или водно-гликолевая смесь), которая направляется в охладитель. В случаях, когда присутствует потребитель тепла, избыточное тепло может быть эффективно использовано. Для этого разработана специальная модель установки Triogen ORC (WBI-Vario), в которой отведенное в конденсаторе тепло может использоваться при температуре до 80 °С. Конечно, с точки зрения выработки электроэнергии, это невыгодно, однако система управления установки имеет функцию для выбора наиболее эффективного режима эксплуатации и выработки электрической мощности в зависимости от потребности.
Силовая электроника и система управления
Для подключения высокооборотного генератора к сети 50 или 60 Гц применяется инвертор, обеспечивающий прямое соединение с трехфазной сетью, 400 В. Основная сеть используется для пуска системы. При этом очень большое значение имеет расположение генератора и основного насоса на одном валу.
Изменение температуры рабочего тела, подаваемого в испаритель, влияет в значительной мере на температуру рабочей жидкости. Система управления изменяет частоту вращения генератора, турбины и насоса для оптимизации потока рабочего тела и получения требуемой температуры на входе в турбину. В результате обеспечивается достаточно стабильная работа с плавными сбросами и набором нагрузки и сохранением высокого КПД практически на всех режимах.
Силовая электроника и контроллер PLC смонтированы в отдельном блоке, который на площадке может быть приспособлен для работы с другим станционным оборудованием.
Энергоустановка Triogen ORC мощностью 160 кВт
После успешного проведения испытаний прототипа установка была адаптирована под различные нужды заказчиков. В настоящее время она включает четыре модуля полной заводской готовности для поставки под ключ:
• стандартный технологический модуль, в который входят: высокооборотный турбогенератор, рекуператор, конденсатор, емкость для хранения рабочего тела, основной насос, клапана, включая трубную обвязку, средства измерения и контроля;
• тепловой модуль, включающий испаритель, который настраивается в зависимости от станционных условий и параметров доступного остаточного тепла и подсоединяется напрямую к источнику остаточного тепла;
• модуль охлаждения, включающий охладители воды для конденсатора (настраивается в зависимости от условий конкретной площадки).
• стандартный модуль силовой электроники и электротехнического оборудования, подключающий генератор напрямую в сеть 50 и 60 Гц, а также система управления.
Технологический модуль
Модуль поставляется заказчикам в полной заводской готовности. Его внешние габариты полностью соответствуют стандартам для транспортировки. Корпус модуля выполнен из нержавеющей стали и покрыт специальным составом для снижения коррозии. Компоненты модуля размещены вертикально. Сверху расположен высокооборотный турбогенератор, после которого рабочая жидкость движется вниз и собирается в специальной емкости для хранения в нижней части модуля (фото 2). Технологический модуль имеет 4 основных подсоединения:
• подвод жидкости и пара для испарителя;
• подвод охлаждающей жидкости для охладителя и отвод тепла;
• электрические кабели для силового инвертора;
• разъем для измерительного и контрольного оборудования системы управления.
Кроме того, технологический модуль может иметь трубную обвязку для дополнительной вентиляции, а также спуска рабочей жидкости в аварийных ситуациях.
На рис. 2 представлена схема интеграции установки Triogen ORC в состав биогазовой электростанции на базе двух энергоблоков мощностью по 800 кВт. Центральное положение занимает технологический модуль. Испаритель подключен к каналу подачи выхлопных газов двигателей с использованием контрольных клапанов, которые закрывают канал подачи выхлопных газов в случае аварийного останова.
Варианты применения установки
Изначально Triogen ORC создавались для утилизации сбросного тепла выхлопных газов двигателей внутреннего сгорания. Однако впоследствии были разработаны варианты, в частности, для использования тепла при сжигании биомассы, остаточного тепла различных технологических процессов. При этом параметры установки зависят от характеристик потока остаточного тепла.
Тепло подается напрямую к рабочему телу, без использования каких-либо дополнительных блоков или материалов, таких как масляный теплоноситель или вода под давлением. Это значительно упрощает конструкцию установки, снижает капитальные затраты и энергопотребление. Кроме того, остаточная тепловая энергия после срабатывания может использоваться для нужд отопления.
Область применения установок Triogen ORC включает:
• газопоршневые двигатели, работающие на природном газе, биогазе, газе мусорных свалок и рудничном газе;
• дизельные двигатели;
• малые газовые турбины;
• энергоблоки тепличных хозяйств, муниципальные котельные;
• котельные на биомассе, древесных отходах;
• сжигание газа мусорных свалок;
• утилизация остаточного тепла технологических процессов на нефтехимических и металлургических предприятиях, стекольных и кирпичных заводах.
Опыт эксплуатации
После успешного завершения опытно-промышленной эксплуатации пилотной установки в течение 4000 часов начались серийные поставки заказчикам. Первая серийная установка Triogen ORC предназначалась для работы в составе электростанции когенерационного цикла на базе газопоршневого энергоблока MWM мощностью 2 МВт. После этого было поставлено еще 19 установок различным заказчикам – их общая наработка к настоящему моменту составляет 200 тыс. часов, надежность оборудования 97 %.
Установки Triogen ORC работают на следующих объектах:
• биогазовые электростанции: семь установок в Нидерландах, две в Чехии;
• электростанции на газе мусорных свалок: две установки во Франции (GDF-Suez), две в Португалии (AdP), одна в Германии;
• электростанции на рудничном газе: одна установка в Чехии;
• прямое сжигание газа мусорных свалок: пилотная установка в Нидерландах, дожиг за газовой турбиной во Франции;
• газопоршневые двигатели на природном газе: одна установка в составе электростанции тепличного хозяйства;
• биодизельная электростанция: одна установка в Нидерландах;
• прямое сжигание твердой биомассы: две установки в Италии.
Кроме того, оформлены заказы и в настоящее время ведутся пусконаладочные работы на десяти установках ORC в Бельгии, Германии, Чехии, Италии и Великобритании.
Заключение
Универсальная концепция установок ORC была разработана специалистами университета Лаапееранта и окончательно оформлена в конечный продукт компанией Triogen B.V. для различных вариантов применения. Компания продолжает конструкторские разработки по дальнейшему совершенствованию оборудования. Мощность первой установки, поставленной заказчику, составляла 145 кВт – на сегодня Triogen ORC имеет мощность 165 кВт. В перспективе планируется представлять на рынок установки в диапазоне мощности 70…1000 кВт.
В настоящее время ведутся работы по расширению сферы применения установок ORC. Совершенствуется конструкция установки, проводятся работы по оптимизации динамики потока рабочего тела в турбине. 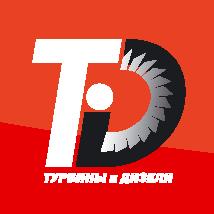
Статья подготовлена по материалам доклада, представленного на конференции Power-Gen Europe-2014, с согласия компании PennWell.