Ян Эймос, Б. Н. Перевай – Siemens AG
Газовая турбина SGT-400 разработана для распределенного производства электроэнергии, которое обеспечивает максимальное приближение генерации к потребителям. Это довольно быстрорастущий рынок, особенно в сегментах промышленных предприятий и нефтегазовых компаний. Основная задача – эффективное производство энергии и надежное энергоснабжение потребителей. Наиболее перспективным при этом является комбинированная выработка электрической и тепловой энергии, поскольку основные барьеры для инвестирования в данную сферу устранены. Высокий общий термический КПД газотурбинных установок последнего поколения, вырабатывающих электроэнергию с утилизацией тепла выхлопных газов, обеспечивает также возможность модернизации сетей центрального теплоснабжения, снижает затраты на электроэнергию для промышленных предприятий.
Для нефтегазового сектора необходимы решения, обеспечивающие энергоснабжение и механическую мощность при поисково-разведочных работах на месторождениях, при добыче и транспортировке нефти и газа в отдаленных районах. Газовые турбины SGT-400 подтвердили высокую надежность при работе в островном режиме, без основной энергосети, на различных видах топлива, с высоким уровнем нагрузки.
В связи с постоянными изменениями на энергетических рынках и специфическими требованиями заказчиков, компания Siemens продолжает масштабные инвестиции в научно-исследовательские и опытно-конструкторские разработки для повышения эксплуатационных параметров SGT-400.
Эксплуатация и варианты применения SGT-400
Общий парк газотурбинных установок SGT-400, находящихся в эксплуатации в настоящее время, насчитывает 300 энергоблоков по всему миру. Их общая наработка составляет более 2500 тыс. часов. Наработка пилотной установки SGT-400 на площадке заказчика уже достигла 100 тыс. часов.
Двухвальная конструкция позволяет применять SGT-400 для выработки электроэнергии и в качестве механического привода в промышленном и нефтегазовом секторе. Наиболее перспективно ее использование в составе электростанций когенерационного цикла для комбинированного производства энергии. Высокая температура выхлопных газов обеспечивает выработку технологического пара с высокими параметрами – в результате увеличивается общий КПД установки.
В качестве механического привода SGT-400 используется в газоперекачивающих агрегатах для транспортировки природного газа по магистральным газопроводам, закачки газа в пласт на морских платформах и в составе наземных компрессорных станций и ПХГ.
Газовые турбины надежно и эффективно работают в любых климатических условиях: от экстремально холодных условий Арктики до жарких условий пустыни. Существуют две модификации установки – мощностью 13 МВт и 15 МВт (рис. 1).
Газовая турбина SGT-400 мощностью 13 МВт представлена на рынке в 1999 г. Пилотная установка была введена в эксплуатацию в когенерационном цикле на площадке нефтеперерабатывающего завода.
Модифицированная версия газотурбинной установки SGT-400 представлена в 2010 г. При ее создании использовались все новейшие разработки и достижения в газотурбостроении. Сравнение характеристик базовой и модифицированной версий ГТУ представлено в табл. 1. Газовые турбины данной модификации были поставлены заказчикам в промышленном и нефтегазовом секторе. Результаты инспекции пилотной установки после эксплуатации в течение 17 тыс. часов подтвердили хорошее состояние модифицированных компонентов, а также заявленные эксплуатационные характеристики.
Основные изменения в модификации ГТУ мощностью 15 МВт
Цель модификации SGT-400 – повысить мощность и КПД установки. Для этого была усовершенствована предыдущая модель вместо разработки принципиально новой конструкции газовой турбины. Обеспечена максимальная унификация компонентов обеих моделей с целью снижения расходов на техническое обслуживание ГТУ в процессе эксплуатации, а также достижения высокого уровня надежности оборудования.
Существует два основных способа повышения мощности газовой турбины – увеличение массового расхода воздуха через двигатель и повышение рабочей температуры в турбине или комбинация обоих методов. Оценка вариантов проводилась с использованием метода Six Sigma с учетом следующих требований:
• повышение мощности ГТУ (на 12 %) вне зависимости от атмосферных условий;
• сохранение низких уровней эмиссии;
• сокращение эксплуатационных расходов;
• максимальная унификация компонентов ГТУ с предыдущей моделью.
Выбранный вариант обеспечивает повышение мощности ГТУ путем увеличения массового расхода воздуха на 13 %. Температура на входе в турбину была оставлена без изменений, что позволило сохранить конструкцию компрессора. При этом степень повышения давления в компрессоре увеличена с 16,8 до 18,9. Компоненты, подвергнувшиеся модернизации, представлены на рис. 2.
Аэродинамическое совершенствование компрессора
Модернизированная версия SGT-400 оснащена осевым компрессором, имеющим 11 трансзвуковых ступеней. Поперечный разрез компрессора представлен на рис. 2. Внешняя стенка корпуса входного подшипника компрессора и статор низкого давления были модернизированы для обеспечения большей площади потока. Диаметр внутренней стенки корпуса подшипника и внешний диаметр диска ротора оставлены без изменений. Конструкция рабочих и направляющих лопаток ступеней низкого давления была доработана, чтобы обеспечить соответствие увеличенному диаметру статора. Доработана также конструкция лопаток ступеней высокого давления. Количество лопаток на каждой ступени оставлено без изменений, но были оптимизированы их аэродинамические характеристики.
Конструкция лопаток нулевой, 1и 2-й ступеней статора и ротора была разработана для эксплуатации при относительно высоком числе Маха на входе. В новой модификации использовались те же принципы конструкции этих лопаток, поскольку аэродинамические характеристики на данных ступенях остались без изменений. Лопатки остальных ступеней (3…10), которые работают при низком числе Маха, имеют конструкцию в виде двойной дуги и профиля С4, как и в предыдущих моделях ГТУ компании Siemens. В модернизированной версии для этих лопаток был выбран диффузорный тип профилей.
На начальном этапе исследований по модификации компрессора был выполнен анализ кривизны линий для оценки свойств и рабочих характеристик направляющих и рабочих лопаток. Использование конструкции компрессора предыдущей модели ГТУ позволило минимизировать изменения компонентов ГТУ, а также применить те решения, которые были отработаны и проверены в эксплуатации на ГТУ SGT-300. В частности, это касается 3D лопаток, применение которых повысило КПД компрессора при работе в широком диапазоне нагрузок и в различных условиях эксплуатации.
При детальном анализе выбранной конструкции использовался метод вычислительной газодинамики. С помощью этого метода проводилось изучение аэродинамических характеристик компрессора и оценка необходимых изменений для обеспечения требуемых параметров рабочих и направляющих лопаток. В частности, анализировалась конструкция канала воздухозаборника компрессора, опоры ротора и облопаченной проточной части.
В результате анализа было подтверждено, что конструкция входного канала обеспечивает необходимое поле скоростей потока и потери во входном канале достаточно низкие. На каждой ступени направляющих и рабочих лопаток концевой зазор был оптимизирован для минимизации потерь. При этом размер зазора рассчитан таким образом, чтобы предотвратить механическое повреждение лопаток, вызванное задеванием за статор.
Ротор и статор компрессора имеют истираемые абразивные уплотнения для оптимизации радиальных зазоров. Результаты анализа подтвердили, что модифицированный компрессор обеспечивает все расчетные параметры по потоку, повышению давления и КПД.
В табл. 2 сравниваются расчетные параметры компрессоров модифицированной и предыдущей версии ГТУ. Для оптимизации аэродинамических характеристик и обеспечения необходимых уровней вибрации лопатки претерпели ряд доработок. При этом был определен диапазон изменений показателя повышения давления (рис. 3) и КПД (рис. 4) последовательно на каждой ступени. На графиках видно, как изменялись показатели в процессе доработок в сравнении с показателями предыдущей версии ГТУ.
Характеристики на переменных режимах
В процессе анализа были определены нерасчетные характеристики компрессора и рабочие диапазоны. Для достижения требуемых показателей в конструкции компрессора применен входной направляющий аппарат с изменяемой геометрией потока, а также 4 ряда регулируемых лопаток.
Параллельно с разработкой конструкции лопаток применялся также анализ с использованием метода конечных элементов (FEA – finite element analysis). На начальных этапах FEA использовался для определения напряжений в лопатках и дисках при стабильном режиме работы. После разработки оптимальной конструкции лопаток и дисков, соответствующей всем необходимым критериям, был применен модальный анализ для расчета возможных режимов и типов вибраций, а также динамических напряжений в лопатках в резонансных условиях.
Проверка механической прочности лопаток компрессора
При разработке модифицированной версии ГТУ использовалась методика хронометража по кончику лопатки с помощью оптического зонда. Во время доводочных испытаний на первых шести ступенях компрессора были установлены восемь оптических датчиков для определения концевого зазора при данном осевом положении. При прохождении кончика лопатки через датчик система регистрировала время для каждой лопатки. Зная скорость и радиус движения каждой лопатки, момент прохождения датчика можно пересчитать для определения отклонения.
Данные, полученные со всех датчиков в определенном положении лопаток, могут использоваться для расчетов таких показателей, как частота, амплитуда, фаза и других вибрационных характеристик. Вибрационные характеристики лопаток всех шести ступеней отслеживались в рамках программы испытаний в режиме реального время на различных эксплуатационных режимах, при различной нагрузке и частоте вращения.
На завершающем этапе полученные в процессе доводочных испытаний данные были нанесены на диаграмму Кэмпбелла для подтверждения того, что линии частоты формы колебаний и линии кратности возбуждения не пересекаются в диапазоне рабочей частоты вращения. Коэффициенты запаса прочности рассчитаны на основе реальных отклонений в отношении к допустимым отклонениям. В результате испытаний не было отмечено никаких значительных отклонений от расчетных значений, и конструкция лопаток была одобрена для применения.
Конструкторская часть проекта
На рис. 5 показаны изменения, которые были внесены в конструктивную часть установки. Крепления лопаток нулевой ступени разработаны с целью упрощения демонтажа лопаток на площадке эксплуатации без снятия ротора. Аналогичная конструкция использовалась и для лопаток предыдущей модели ГТУ.
В процессе модификации доработана конструкция лопаток нулевой ступени, чтобы минимизировать повреждения в случае попадания инородных предметов (или льда). Все рабочие и направляющие лопатки, а также диски компрессора, входной и выходной валы изготавливаются из тех же материалов, что и в предыдущей версии.
Лопатки ротора и статора компрессора имеют необрастающие покрытия, за исключением лопаток ротора нулевой и первой ступеней, имеющих покрытия TiN для минимизации коррозии, эрозии и защиты от ударных воздействий. Корпус ступеней низкого давления и корпус входного подшипника модифицированы в связи с увеличением диаметра проточной части компрессора. Конструкция компрессора высокого давления оставлена без изменений, использован статор компрессора высокого давления турбины SGT-300.
Центральный корпус изготавливается из стали с содержанием Cr для повышения сопротивления ползучести, поскольку температура на выходе компрессора увеличена на 12 °С. Для снижения теплоотдачи на корпусе газогенератора применяются теплоизоляционные покрытия, в результате чего продлен срок службы компонентов.
Конструкция ротора газогенератора и силовой турбины оставлена без изменений. В связи с повышением частоты вращения ротора и увеличением изгибающего момента диаметр крепежных болтов был увеличен до 31 мм.
Цель модернизации – увеличение срока эксплуатации и надежности ГТУ, поэтому конструкция упорных подшипников скольжения была оптимизирована (рис. 6). Изменен процесс обработки корпуса подшипников силовой турбины для установки модифицированных подшипников.
В конструкцию камеры сгорания существенных изменений не вносилось. Были оптимизированы ее эксплуатационные параметры, чтобы разделить поток воздуха на пилотную и основные горелки и обеспечить требуемые температуры в основной зоне горения для поддержания нужных уровней эмиссии CO и NOx. Кроме того, увеличен расход топлива для достижения мощности 15 МВт. В процессе доводочных испытаний были подтверждено, что низкоэмиссионная камера сгорания обеспечивает требуемые уровни эмиссии при работе на газообразном и жидком топливе на всех режимах.
Конструкция турбины газогенератора оставлена без изменений. Первая ступень турбины оснащена монокристаллическими лопатками, вторая – лопатками с внутренними покрытиями из сплава. Данные лопатки подтвердили высокую устойчивость к коррозии. В связи с повышением рабочих температур изменен материал, из которого изготавливается корпус турбин.
В связи с повышением расхода газа была увеличена пропускная способность газовой турбины. Это достигнуто путем модификации конструкции соплового аппарата силовой турбины.
Доводочные испытания
На финальной стадии создания модифицированной версии SGT-400 был изготовлен прототип двигателя и проведены его доводочные испытания на испытательном стенде компании в г. Линкольн (Великобритания).
В процессе испытаний использовалось большое количество контрольно-измерительной аппаратуры для подтверждения расчетных параметров. Двигатель был оснащен датчиками температуры, давления, расходомерами для контроля основных показателей. Были проведены также предварительные испытания двигателя на соответствие базовым требованиям, а именно:
• запуск двигателя проходит успешно;
• выход на номинальную нагрузку проходит без сбоев;
• достигается номинальная частота вращения;
• отсутствуют значительные резонансные колебания лопаток и вибрация ротора;
• достигнут номинальный расход воздуха в компрессоре, подтверждено расчетное значение КПД компрессора;
• подтверждено расчетное значение термического КПД двигателя.
Результаты испытаний показали, что двигатель удовлетворяет требованиям по всем позициям.
Эксплуатационные испытания
Сопловой аппарат первой ступени силовой турбины регулирует поток воздуха через двигатель, и поэтому крайне важно, чтобы скорость потока через него соответствовала частоте вращения ротора компрессора и уровню расхода рабочего тела. Повышение пропускной способности соплового аппарата первой ступени достигается изменением профиля расположения направляющих лопаток для увеличения сечения соплового аппарата и угла установки лопаток.
Основное внимание было направлено на достижение расчетных параметров турбины газогенератора. Было определено, что зазор у лопаток первой и второй ступеней можно уменьшить, что позволит оптимизировать потери через радиальные зазоры. После уменьшения зазоров (по итогам испытаний относительно проектных решений) КПД был достигнут на уровне расчетных значений.
На рис. 7 сравниваются параметры двух модификаций SGT-400. Из графика видно, что выполненные работы обеспечили требуемое повышение параметров ГТУ при сохранении частоты вращения ротора компрессора и температуры на входе в турбину. В табл. 3 приведено сравнение параметров SGT-400 мощностью 13 МВт, расчетных значений и реальных параметров ГТУ мощностью 15 МВт, которые были достигнуты в процессе доводочных испытаний.
Пэкидж ГТУ
В концепцию разработки N-пэкиджа для газотурбинной установки SGT-400 заложены следующие принципы: максимальная заводская готовность, удобство в обслуживании и эксплуатации.
В результате оптимизировано рабочее пространство для обслуживающего персонала за счет расположения систем жидких сред с входами/выходами у границ рамы и удаления нагретых частей из зоны прямого доступа во избежание несчастных случаев в результате контактов. Изменено также расположение площадок обслуживания.
Электрические, управляющие компоненты и интерфейсы размещены со стороны газовой турбины, противоположной расположению генератора. Это уменьшает воздействие вредных факторов на качество работы обслуживающего персонала. Также сократилось число интерфейсов между ГТУ и системами заказчика. Одно из основных требований при разработке модифицированной версии SGT-400 – максимальная унификация компонентов, для того чтобы можно было использовать существующий пэкидж. Модифицированная ГТУ имеет ту же площадь основания и идентичные присоединительные размеры. Модернизация пэкиджа SGT-400 позволила сократить время монтажа энергоблока на площадке заказчика. Были сохранены компактные размеры и сравнительно малый вес. Компоненты SGT-400 , которые были модифицированы и которые остались без изменений, представлены на рис. 8.
Топливная гибкость
Одной из важнейших задач при разработке газовых турбин является обеспечение топливной гибкости. В частности, для нефтегазовых компаний очень важно, чтобы ГТУ могли работать на газе с высоким содержанием инертных газов, таких как азот (N2) и углекислый газ (CO2), попутном нефтяном газе и др. В настоящее время SGT-400 обеспечивает надежную работу на газах с содержанием инертных компонентов до 40 %. График применяемости различных видов топлива в газотурбинных двигателях SGT-400 представлен на рис. 9.
Направление дальнейших разработок – возможность использования газов с высоким содержанием водорода, а также других топливных смесей, таких как газ доменных печей и синтез-газ. Разработки выполняются на основе опыта и результатов эксплуатации других газотурбинных установок компании Siemens.
ГТУ SGT-400 оснащена камерой сгорания, работающей на предварительно обедненной топливной смеси, что гарантирует низкие уровни эмиссии и, соответственно, выполнение любых региональных экологических норм.
Передовая система управления и контроля процессов горения обеспечивает надежную и эффективную эксплуатацию газотурбинной установки независимо от изменений атмосферных условий и состава топлива.
Техническое обслуживание
График технического обслуживания ГТУ SGT-400 (рис. 10) достаточно гибкий. Он включает ежегодные технические инспекции состояния оборудования на площадке эксплуатации, замену компонентов горячей проточной части каждые три года. Плановый ремонт двигателя проводится через шесть лет. При этом с целью сокращения времени простоя электростанции, компания может предоставить двигатель для замены на срок проведения ремонтных работ.
Специалисты компании Siemens постоянно отслеживают и анализируют работу поставленного оборудования на площадках заказчиков. Полученные результаты используются для дальнейшего совершенствования газотурбинных установок с целью достижения максимальной надежности и готовности к эксплуатации. Надежность ГТУ SGT-400 по результатам мониторинга составляет 97 %.
Заключение
На данный момент компания Siemens готова предложить своим заказчикам две модификации ГТУ SGT-400 – 13 МВт и 15 МВт.
Основным отличием 15 МВт-й версии является более высокий электрический КПД, который удалось достичь за счет совершенствования компонентов газовой турбины в процессе модернизации.
При этом у заказчика появилась возможность выбирать в диапазоне мощности оптимальный вариант под определенный тип термодинамического цикла. Опыт эксплуатации SGT-400 мощностью 15 МВт подтвердил расчетные сроки службы основных компонентов горячей проточной части и надежность работы газотурбинной установки в целом. 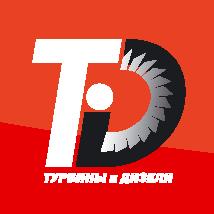