А. Л. Сабуров, А. Е. Чубарь – ООО «Сименс» В. Д. Воронин – ООО «РН-Туапсинский НПЗ»
Энергоснабжение нефтеперерабатывающего предприятия, расположенного в курортной зоне Черноморского побережья, – непростая задача, которую решили специалисты компании Siemens, применив современные двухтопливные газотурбинные установки SGT-800 мощностью по 47 МВт.
В 2007 г. компанией «Роснефть» был утвержден план и начата реконструкция нефтеперерабатывающего завода в г. Туапсе (Краснодарский край) с целью увеличения выпуска продукции до 12 млн тонн/год вместо нынешних 4 млн тонн, с увеличением глубины переработки сырой нефти до 95 %. Реконструкция и строительство нового объекта ведется на территории существующего НПЗ. Это, с одной стороны, обусловлено близостью порта и нефтеналивного терминала «РН-Туапсенефтепродукт» в г. Туапсе, но с другой стороны, накладывает существенные ограничения на проведение работ и предъявляет самые строгие требования к планированию и управлению проектом.
Дополнительные сложности связаны с географией самого объекта строительства, а также с количеством и расположением подъездных путей, площадок хранения оборудования. Завод расположен на небольшой площади, ограниченной с одной стороны путевым хозяйством грузовой станции НПЗ и рекой Туапсе, с другой – горным массивом. Склады хранения принимаемого нового оборудования находятся вне территории объекта реконструкции.
В рамках данного проекта требовалось обеспечить новые нефтеперерабатывающие установки технологическим паром, а также существенно возросшее энергопотребление. Частью проекта реконструкции завода предполагалась модернизация существующей на его территории паротурбинной ТЭЦ с заменой установленных турбин агрегатами единичной мощностью 45…55 МВт (6 агрегатов).
ГТУ должны применяться совместно с паровыми котлами-утилизаторами, с выработкой технологического пара на нужды НПЗ. Параметры вырабатываемого пара: давление 4 МПа, температура 440 °С. Рабочая схема вновь планируемой ГТУ–ТЭС предполагает эксплуатацию энергоблоков по схеме 4+2, где два агрегата находятся в постоянном горячем резерве. Все утилизационные котлы работают на общий коллектор технологического пара. Новую ТЭС, помимо обеспечения основного потребителя – НПЗ, планировалось использовать в виде резервной электростанции для проведения Олимпийских игр в Сочи в 2014 году, а также для выработки электроэнергии для выдачи ее во внешнюю сеть.
По аналогии с модернизацией самого НПЗ, реконструкция ТЭЦ проводилась в тех же условиях: крайне стесненная площадка строительства, необходимость поддержания в работе существующей ТЭЦ до момента готовности первой пусковой очереди, а также внешние факторы – субтропический климат, высокая сейсмическая активность района.
Одним из важнейших решений, направленных на оптимизацию проекта, стало применение энергоблоков модульного исполнения на открытой площадке. Это позволило отказаться от возведения машинного зала ТЭС и разместить значительную часть технологического оборудования под открытым небом. В результате снизились капитальные затраты и сократились расчетные сроки строительства. Помимо этого, такое решение способствовало более эффективному использованию ограниченного пространства строительной площадки. Нужно отметить, что такой подход является достаточно уникальным для российской практики возведения объектов электрогенерации.
При выборе ГТУ заказчик сформулировал основные требования к газотурбинным энергоблокам: двухтопливные, с автоматическим переключением с одного вида топлива на другое, возможность продолжительное время работать на дизельном топливе. Установки должны обеспечить устойчивую работу в режиме от 5 % до 100 % мощности, регулирование паропроизводительности, выдерживать значительные сбросы/набросы нагрузки. Кроме того, они должны занимать минимальную площадь застройки, иметь низкий уровень выбросов NOx и CO, сейсмостойкость 9 баллов. Время пуска должно составлять не более 7 минут.
Компания Siemens участвовала в конкурсе с предложением энергоблоков на базе SGT-800A единичной установленной мощностью 47 МВт. Данная ГТУ является одной из последних разработок компании в области промышленных турбин, предназначенных для выработки электроэнергии. Технические характеристики ГТУ оптимально подходят для решения задач по снабжению электроэнергией и технологическим паром реконструированного Туапсинского НПЗ, а именно:
• значительная мощность агрегата – 47 МВт (эл.);
• высокий КПД в простом цикле – 38 %;
• выхлоп с высокой температурой отходящих газов (до 550 °C), что позволяет использовать утилизационные котлы различных типов и конструкций без необходимости применять систему дожигания;
• низкий уровень вредных выбросов, что крайне важно в данном случае, так как объект расположен на Черноморском побережье Краснодарского края, имеющем важное рекреационное значение и потому требует особого внимания к соблюдению экологических норм;
• современная система автоматического управления, отвечающая лучшим мировым стандартам и позволяющая добиться высокой эффективности работы ТЭС за счет оптимального управления всеми этапами технологического процесса;
• высокая надежность газотурбинного двигателя и его систем, основанная на многолетнем опыте Siemens;
• возможность работы ГТУ на различных видах газового и жидкого топлива без необходимости переналадки;
• программы сервиса и технологического усовершенствования ГТУ. Помимо широких возможностей сервисной поддержки заказчика на всех этапах жизненного цикла ГТУ, компания постоянно работает над улучшением SGT-800, открывая возможность модернизации приобретенных двигателей с применением передовых технических решений, а это, в свою очередь, позволяет заказчику эксплуатировать наиболее современную и эффективную технику.
Газовая турбина SGT-800 имеет модульную конструкцию с минимальным количеством компонентов в одновальной конфигурации и ротором, рассчитанным на рабочую частоту вращения 6600 об/мин. Ротор компрессора и трехступенчатый узел турбины образуют единый вал, установленный в стандартных гидродинамических подшипниках с самоустанавливающимися сегментами.
Привод генератора осуществляется с холодной стороны газовой турбины, обеспечивая простую и оптимальную компоновку выхлопа. Конструкция камеры сгорания позволяет отдельно снимать каждую из 30 горелок без разборки всего агрегата, что также обеспечивает простой и удобный осмотр камеры сгорания. ГТУ может легко извлекаться из укрытия для проведения ремонта. Для этого вал между редуктором и газовой турбиной отсоединяется, и входная камера сдвигается в сторону генератора. При замене отдельных лопаток компрессора или турбины на месте эксплуатации предусматривается трехплоскостная балансировка ротора (диск № 1 компрессора, промежуточный вал и диск № 3 турбины).
Компрессор – трансзвукового типа, 15-ступенчатый, со степенью сжатия 20 (согласно ISO); имеет современную аэродинамическую конструкцию. Для достижения высокой эффективности используется технология управляемой диффузионной аэродинамической поверхности. Первые три ступени имеют изменяемую геометрию. Для минимизации утечек над концами лопаток в ступенях 4–15 используются истираемые уплотнения. Держатель крыльчатки в секции высокого давления ступеней 11–15, где самые короткие лопатки, изготовлен из материала с низким коэффициентом теплового расширения, что обеспечивает минимальные зазоры. Ротор компрессора выполнен из дисков, сваренных в надежный блок с применением электронно-лучевой сварки.
Камера сгорания – кольцевого типа, имеет сварную конструкцию из листового металла. Теплоизолированное покрытие внутренней поверхности КС снижает уровень теплопередачи и увеличивает срок службы камеры сгорания. Такая концепция конструкции много лет используется в газовых турбинах, производимых компанией Siemens.
Камера оснащена 30 горелками типа DLE третьего поколения. Эта технология обеспечивает уровень выбросов оксидов азота и углекислого газа менее 15 ppm (при 15 % O2) при работе на природном газе и 42 ppm – на жидком топливе, без использования впрыска воды или пара. Сухое подавление вредных выбросов также применяется при работе с двухтопливной системой.
Трехступенчатая турбина, изготовленная в виде единого модуля для облегчения технического обслуживания, имеет болтовое соединение с валом компрессора. Аэродинамические поверхности направляющих и рабочих лопаток 1и 2-й ступеней охлаждаются с помощью технологии, используемой в других газовых турбинах Siemens. Первая лопатка выполнена из монокристаллического материала, что обеспечивает высокую надежность и долгий срок службы.
Фланцы статора турбины охлаждаются воздухом из компрессора для уменьшения зазоров и повышения эффективности. Размещение приводимого агрегата с холодной стороны позволяет осуществлять осевой выхлоп через диффузор, обеспечивая наилучшие характеристики ГТУ. Для минимизации аэродинамических потерь при работе турбины в составе станции комбинированного цикла или совместном производстве тепла и электроэнергии (когенерация) с особой тщательностью разработана конструкция соединения выхлопного диффузора и котла-утилизатора.
В целях защиты обслуживающего персонала предусмотрена наружная изоляция ГТУ для снижения температуры незащищенных поверхностей и максимально возможного подавления шума внутри укрытия. Обшивка применяется начиная с 3-й ступени компрессора на холодной стороне, включает горячую секцию и диффузор выхлопа.
Газовая турбина SGT-800 запускается с помощью пускового электродвигателя, подключенного к понижающему редуктору. Компрессор оснащен двумя перепускными (противопомпажными) клапанами в 5и 10-й ступенях, они открыты в начале процесса запуска и закрываются при запуске турбины. Во время эксплуатации выходная мощность установки регулируется с помощью направляющего аппарата и за счет изменения температуры сгорания.
В энергоблоке применяется генератор переменного тока производства компании АВВ (Швеция). Генератор AMS 1250 A LF – синхронный, 4-полюсный, с бесщеточной системой возбуждения, с сопротивлением в цепи заземления нейтрали. Электрическая мощность генератора составляет 56,25 МВА, напряжение 11 кВ.
Система охлаждения маслосистемы газовой турбины и генератора – прямая, воздушная. В состав энергоблока входит двухступенчатое комплексное воздухоочистительное устройство. ГТУ оснащена всеми необходимыми системами – вентиляции и пожаротушения, маслоснабжения и охлаждения масла, системой подачи и регулирования топлива, промывки компрессора, обнаружения загазованности, системой управления и др. Оборудование энергоблока поставляется в звукотеплоизолированном контейнере.
Нужно отметить, что предложенная модификация газовых турбин SGT-800A находилась в производстве на момент заключения контракта. В настоящее время компания Siemens может предложить уже три модификации данного агрегата:
• SGT-800A наружного/внутреннего типа установки, единичной мощностью 47 МВт согласно ISO;
• SGT-800B наружного/внутреннего типа установки, единичной мощностью 50 МВт согласно ISO;
• SGT-800B2 модульного исполнения, единичной мощностью 50 МВт. Данная модификация поставляется в полной заводской готовности, что сокращает время монтажных и пусконаладочных работ. Она может применяться как на сухопутных, так и на морских объектах.
Проект новой ТЭС предполагает две пусковые очереди – по три энергоблока каждая очередь. Также планируется установить паровые противодавленческие турбины марки ПТ-12 мощностью по 12 МВт производства ОАО «Калужский турбинный завод».
Площадка строительства ТЭС расположена на территории самого завода. В связи с этим при разработке проекта заказчик предложил установить оборудование станции в соответствии с требованиями ВНТП 81-85 для производственной зоны нефтеперерабатывающего предприятия.
Для выполнения данного требования проектом был предусмотрен подъем воздухозаборных устройств циклового воздуха ГТУ, а также всех вентиляционных систем энергоблоков, включая выброс вентиляции, на высоту не менее 20 метров. Также для выполнения этого требования потребовалась заменить большую часть оборудования на взрывозащищенное. Впоследствии заказчик, с целью снижения капитальных затрат на строительство, частично пересмотрел требования к строящейся ТЭС за счет усиления мер по взрыво- и пожаробезопасности на территории НПЗ.
Одной из особенностей данного проекта стало требование заказчика к возможности эксплуатации оборудования на двух видах топлива – дизельном и природном газе. Дизельное топливо являлось основным при вводе первой пусковой очереди. Первоначальные результаты эксплуатации ГТУ на жидком топливе показали, что необходима оперативная доработка топливной системы, которая и была выполнена компанией Siemens совместно с персоналом эксплуатирующей организации.
Примечательно, что эти работы не привели к существенным отклонениям от запланированных показателей генерации ТЭС, так как в процессе доработок эксплуатация ГТУ осуществлялась на природном газе. Это стало возможным благодаря тому, что заказчик обеспечил ранний ввод в эксплуатацию газопровода среднего давления, а также хорошо продуманной организации самого процесса доработки.
Для обеспечения гибкости эксплуатации ТЭС при выработке электроэнергии и технологического пара была рассмотрена и применена схема с регулируемым байпасом парового котла-утилизатора. Производство технологического пара обеспечивает паровой котел-утилизатор горизонтального типа, изготовленный компанией «ЭМАльянс» в партнерстве с Nooter-Eriksen. Для максимально компактного размещения энергоблока с котлом данного типа был применен байпас с вводом продуктов сгорания ГТУ при перепуске котла-утилизатора обратно в основную дымовую трубу. При этом байпасный канал вывешен на опорных конструкциях самого КУ.
Чтобы обеспечить максимальную гибкость эксплуатации агрегата при заданной выработке пара и электроэнергии, а также сделать застройку как можно более компактной, применен перепускной клапан с плавным управлением створкой. Такое управление клапаном обеспечивается установленной гидравлической системой перемещения створки с аварийным аккумулятором давления.
Необходимо отметить, что все проектные работы, связанные с установкой байпасного клапана, были проведены собственными силами российского подразделения Siemens. Сам клапан также произведен компанией Siemens, в частности, подразделением NEM Power Systems, в настоящий момент входящим в состав компании.
Для того чтобы обеспечить равномерное расходование эксплуатационного ресурса каждого энергоблока, в системе управления энергоблоками установлен контроллер распределения нагрузки. Он может перераспределять нагрузку между энергоблоками, находящимися в эксплуатации, а также оперативно менять режим работы каждого из них в соответствии с уставками оператора по вырабатываемой электроэнергии или же автоматически, в соответствии с изменениями условий работы ГТЭС. Основной принцип, соблюдаемый при этом, – равномерное расходование эксплуатационного ресурса каждым блоком.
Генеральным проектировщиком ГТЭС выступил «Ростовтеплоэлектропроект» – филиал ОАО «Южный ИЦЭ». Проектом предусмотрено традиционное рядное размещение энергоблоков, где со стороны генераторов установлены повышающие трансформаторы 10/100 кВ мощностью 63…80 МВА, на стороне выхлопа – утилизационные котлы с этажерками вспомогательного оборудования.
Электроснабжение потребителей завода производится через две понижающие подстанции ГПП-1/2.
Район строительства располагается в зоне с максимальной возможной сейсмической активностью 9 баллов по шкале MSK-64, поэтому устанавливаемое оборудование должно было отвечать высоким требованиям по сейсмостойкости в соответствии с СНКК 22-301-2000. Учитывая, что электростанция в целом является объектом повышенного уровня ответственности, обеспечение ее сейсмостойкости включало не только мероприятия по недопущению возможных разрушений, но и по сохранению работоспособности оборудования как в момент расчетного землетрясения, так и после него.
Цикл работ по выполнению требований сейсмостойкости включал в себя сейсмическое микрорайонирование площадки строительства, расчетное и экспериментальное обоснование конструктивных мер по обеспечению сейсмостойкости оборудования и строительных конструкций, аттестацию оборудования специализированными организациями. При этом, с целью оптимизации затрат, заказчиком и генеральным проектировщиком объекта было принято решение о комплексном подходе к формулированию требований по сейсмостойкости к конкретным элементам технологического оборудования.
Идея комплексного подхода заключается в том, что в рамках всего объекта выделяются технологические единицы, оборудование которых в свою очередь подразделяется на различные группы ответственности по влиянию возможных отказов на технологический процесс объекта в целом.
Такой подход позволяет оптимизировать применение требований по сейсмостойкости, снижая их в обоснованных случаях без ущерба для выполнения технологических функций ТЭС, а также обеспечивая высокую степень устойчивости электростанции к сейсмическим воздействиям при одновременном снижении капитальных затрат на ее строительство. Аналогичные методы определения сейсмических требований к проекту применяются в атомной промышленности, но в данном случае подобный подход можно назвать уникальным.
Примером комплексного обеспечения требований по сейсмостойкости, условиям размещения оборудования, удобству обслуживания и компактности является проект быстровозводимого здания для блочного оборудования, выполненный специалистами российского подразделения Siemens совместно с рядом контрагентов. Ряд технологического оборудования энергоблоков был компактно размещен в индивидуальных легкосборных зданиях на территории ТЭС.
Такое размещение не только обеспечило оптимальные условия для обслуживания и эксплуатации оборудования, но и в ряде случаев позволило снизить требования к сейсмостойкости установленных устройств за счет использования строительных конструкций здания для демпфирования расчетных сейсмических воздействий при вероятном землетрясении. Полное демпфирование сейсмического воздействия строительными конструкциями здания предусмотреть невозможно, поэтому применяемое оборудование должно быть способно выдержать остаточное динамическое воздействие (что подтверждается испытаниями установленного оборудования у изготовителей).
Аналогичный подход применяется и при изготовлении самого энергоблока: сейсмическое воздействие демпфируется опорной рамой и ее элементами, остаточное динамическое воздействие воспринимается или непосредственно установленными в энергоблоке системами, способными выдержать подобное воздействие, или же вибропоглощающими опорами и подвесами конкретного узла или системы. Для каждой технологической единицы решения разрабатывались индивидуально в рамках описанного выше комплексного подхода. Так, в отношении аппаратов воздушного охлаждения масла ГТУ применялись иные способы обеспечения сейсмостойкости, такие как использование пружинного подвеса всей установки АВОМ энергоблока с применением демпферов колебаний. 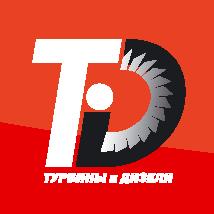