Сара Аллен, Нигель Дафт – Brush Electrical Machines Ltd. (Великобритания)
В рамках основной производственной программы компания Brush изготавливает электрогенераторы для мобильных энергетических установок. Всего в настоящее время заказчикам по всему миру поставлено более 350 генераторов данного типа. Поскольку такие генераторы устанавливаются на трейлеры, существуют жесткие ограничения по их массе и габаритам для возможности транспортировки по автомобильным дорогам.
Для разработки максимально компактного пэкиджа были выбраны модели генераторов, обеспечивающие повышение температуры на обмотках ротора и статора в диапазоне, предусмотренном требованиями класса F. Номинальная мощность генераторов при частоте 50 Гц и напряжении 11,5 кВ составила 29,5 МВА.
Для создания конкурентных преимуществ оборудования на энергетическом рынке было принято решение о начале конструкторских разработок с целью повышения мощности генераторов без изменения (а затем и сокращения) массогабаритных показателей пэкиджа.
Проведенные исследования рынка показали, что необходимо также снижение шума до 81 дБ при частоте 50 Гц. В настоящее время генераторы обеспечивают шумовую нагрузку 85 дБ при частоте 50 и 60 Гц.
При оптимизации конструкции генераторов рассматривалось большое количество компонентов, но основное внимание было направлено на температуру обмоток ротора и статора, поскольку данный параметр должен соответствовать международным стандартам: IEC 60034 для частоты 50 Гц и IEEE C50.12 – для частоты 60 Гц.
В связи с тем что в настоящее время в эксплуатации находится большое количество генераторов Brush, в распоряжении специалистов была обширная база данных по результатам испытаний и эксплуатации оборудования. Информация использовалась для анализа и определения компонентов, которые должны быть модернизированы и оптимизированы для соответствия поставленным задачам при соблюдении всех международных технических стандартов. В процессе работ стало очевидно, что для этого необходимо обеспечить оптимальный контроль распределения потоков охлаждающего воздуха внутри генератора.
С электротехнической точки зрения, наиболее простым способом повышения мощности генератора является увеличение количества меди, используемой для изготовления ротора и статора. С учетом конечного веса, количество активного материала для сердечников ротора и статора должно быть сокращено до минимума, чтобы исключить возможность перевозбуждения (увеличения магнитного потока) применяемых материалов.
Это приводит к несоответствию электрической и механической конструкции в отношении прочности генератора, в частности ротора, который должен выдерживать превышение частоты вращения на 25 % при проведении испытаний на предприятии-изготовителе.
В связи с реально существующими противоречивыми конструктивными ограничениями, необходимо было выработать и согласовать оптимальную электрическую и рабочую механическую часть конструкции. Окончательный вариант конструкции генератора был принят после длительных обсуждений и доработок, в которых приняли участие специалисты подразделений компании Brush в г.г. Лафборо (Великобритания) и Пльзень (Польша). В итоге было подтверждено, что все возможные варианты оптимизации учтены и все возможности для проверки правильности принятых проектных решений использованы.
Для моделирования процессов, происходящих в роторе, использовалось программное обеспечение ANSYS, чтобы подтвердить правильность доработок в обмотке ротора. Были проанализированы напряжения, возникающие в зубе ротора, межпазовых клиньях и бандажном кольце ротора.
Увеличение количества меди в составе ротора требует тщательной проверки параметров намагничивания. Для оптимизации указанных параметров применялись три различные методики: проектно-конструкторская программа для оптимизации конструкции генератора, программа SLIM и программное обеспечение ANSYS Maxwell. Для последней программы необходимо было создать компьютерную модель ротора для построения кривой открытого контура цепи путем изменения уровней возбуждения в катушках обмотки ротора.
В процессе разработки выяснилось, что, хотя вентилятор и обеспечивает достаточный поток воздуха через генератор, необходим дополнительный объем охлаждающего воздуха, поскольку при проведении финальных испытаний было отмечено незначительное превышение температуры. В связи с этим решено было установить еще один вентилятор, который обеспечит при необходимости увеличение потока воздуха на 10 %.
Конструкция вентилятора соответствует всем требованиям, приведенным в руководстве Axial flow fans and ducts (R.A. Wallis). Данные по требуемому повышению давления и объему потока были трансформированы в безразмерные коэффициенты с учетом диаметров вентилятора и центрального тела, а также частоты вращения. На основании начальных расчетов по КПД были определены средний коэффициент завихрения и коэффициент повышения среднего общего давления. С использованием метода последовательных итераций определены значения КПД и среднего давления.
При определении КПД вентилятора были рассчитаны и учтены потери, возникающие в связи с зазором между кончиками лопаток и корпусом, относительной длиной лопаток, асимметрией и неоднородностью входного воздушного потока.
Вентилятор разработан для обеспечения постоянного повышения статического давления вдоль оси лопатки. В результате созданы лопатки с закрученным профилем. Была устранена возможность срыва потока в вентиляторе путем снижения максимального коэффициента подъемной силы, а также повышением прочности лопаток до значения 1,0. Методом конечных элементов с использованием программы ANSYS Mechanical 15.0 рассчитаны максимальные уровни напряжений. Было подтверждено, что расчетные показатели напряжений находятся ниже критических, что обеспечивает достаточный уровень надежности.
Вентилятор оснащен лопатками F-series с овальным аэродинамическим профилем, с искривлением носовой части в соответствии со стандартом NACA 230. Кривизна профиля лопатки, ее толщина и отклонение носовой части были отрегулированы с целью оптимизации рабочих характеристик.
Увеличение воздушного потока на 6 % достигнуто путем увеличения количества лопаток и длины хорды по сравнению с предыдущей модификацией вентилятора при сохранении пределов нагрузки на лопатки. Ранее, в связи с ограничением рабочей площади, невозможно было достичь планируемого увеличения воздушного потока на 10 %.
Другим направлением модификации было снижение шума и уменьшение массы генератора. Опыт эксплуатации генераторов большой мощности показал, что необходимое снижение шума достигается за счет покрытия внутренней поверхности корпуса статора звукопоглощающим материалом. Это было использовано в процессе конструкторских разработок.
Для снижения массы генератора и повышения прочности станины статора было решено изменить форму корпуса с квадратной на закругленную. Были подготовлены трехмерные CAD-чертежи корпуса и проведен анализ ANSYS: необходимо было убедиться в том, что при изменении формы корпуса не возникнет проблем с его изготовлением. Кроме того, было подтверждено, что требуемое снижение массы компонентов будет достигнуто.
Поскольку при повышении мощности генератора существенно увеличатся нагрузки на различные узлы и компоненты, проведен дополнительный анализ материалов, из которых данные компоненты изготовлены. Особое внимание уделялось материалу, из которого изготавливается крайний пакет сердечника. В результате анализа решено было заменить материал прижимной пластины: вместо свариваемой стали использовать литейную латунь.
После доработки механических, электрических и тепловых аспектов был проведен анализ FMEA (Failure Mode and Effect Analysis – анализ характера и последствий отказов). Это было необходимо для того, чтобы на начальном этапе выявить проблемы, которые могут возникнуть при производстве генераторов, и иметь достаточно времени на поиск их решения. Кроме того, весь производственный персонал ознакомили с изменениями в конструкции генератора, чтобы можно было задать любые вопросы конструкторам по новой продукции.
Производство новых генераторов планируется на всех производственных площадках компании Brush, в связи с этим была проведена оценка возможностей всех подразделений компании.
С момента начала производства пилотных образцов генераторов группа разработчиков присутствовала на всех этапах процесса, чтобы оперативно решать возникающие вопросы, а также осуществлять доводку конструкции компонентов. В конце каждого этапа производства генератора проводилось взвешивание компонентов и контроль соответствия их конструкции проектной документации.
Как отмечено ранее, особое внимание уделялось распределению потока охлаждающего воздуха. При этом, кроме модификации вентилятора, был оптимизирован профиль воздушного потока, чтобы он охватывал всю поверхность генератора и обеспечивал требуемый уровень охлаждения. С помощью программы ANSYS CFX, а также специальной программы по оценке теплопроводности были разработаны специальные направляющие пластины для оптимального распределения потока.
На начальных этапах моделирование генератора проводилось с помощью плоскостей симметрии или моделировались отдельные компоненты. При этом очень трудно было смоделировать процесс в комплексе. Поэтому решили создать комплектную модель генератора до начала и после выполнения доработок конструкции. Были смоделированы также лопатки вентилятора, чтобы получить объективную картину распределения потока охлаждающего воздуха по модели генератора. Компьютерная CFD-модель состояла из 57 миллионов элементов и была реализована с использованием одновременно восьми компьютеров.
Испытания и анализ модифицированного генератора проводились в течение нескольких недель с целью оптимизации воздушного контура и акустической сигнатуры. Начальные испытания проходили на такой же мощности, как и у существующих генераторов. Это позволило оценить эксплуатационные параметры модифицированного генератора в соответствии с результатами испытаний, а также сравнить их с параметрами существующих генераторов. Кроме того, были определены перспективные возможности модифицированной модели.
Окончательные испытания проводились в присутствии независимых экспертов. В результате испытаний было подтверждено, что модифицированный генератор обеспечивает снижение уровня шума с 85 до 81 дБ и повышение мощности на 15 % при частоте тока 50 Гц. Кроме того, на 3 % была снижена общая масса генератора. 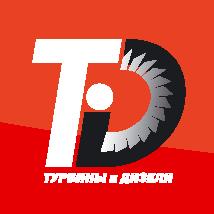