В.В. Дурыманов, C. А. Леонтьев – ООО «Сименс»
В.В. Седов – ОАО «Газпром»
Э.Г. Васильев – ООО «Газпром трансгаз Ухта»
29 декабря 2010 г. исполняется 4 года со дня ввода в эксплуатацию шести ГПА «Балтика-25» на магистральном газопроводе СРТО – Торжок, три из них эксплуатируются на Ухтинской КС и три –- на Вуктыльской КС (ООО «Газпром трансгаз Ухта»). И хотя 4 года – срок небольшой по меркам ресурсных показателей современных ГТУ, сейчас, в канун 2011 года, самое время подвести некоторые итоги и обсудить перспективы применения данного агрегата в России и СНГ.
Надежность работы газотранспортной системы ОАО «Газпром» возможна только при длительной безотказной работе более 4000 имеющихся газоперекачивающих агрегатов. Так, газовая турбина фирмы Siemens SGT-600 в составе ГПА «Балтика-25» показала в плане надежности впечатляющие результаты – за 4 года работы на 6 агрегатах не было ни одного аварийного останова по причинам, связанным с отказом ГТУ.
Агрегаты «Балтика-25» на компрессорных станциях ООО «Газпром трансгаз Ухта» являются первыми ГПА, созданными на базе промышленных ГТУ SGT-600 международного концерна Siemens AG и произведенными в России в тесной кооперации западных и российских компаний для нужд Газпрома. Задачей данного проекта является отработка технологических и логистических цепочек для последующего развертывания локального производства ряда систем агрегата и сборки всего ГПА на территории РФ. Необходимость локального производства и агрегатирования (packaging) обусловлена принятой в ОАО «Газпром» политикой технологической безопасности, направленной на использование на всех объектах газовой отрасли оборудования только российского производства.
Среди характеристик ГПА, названных эксплуатирующей организацией определяющими при выборе оборудования, стали следующие:
• большой межремонтный ресурс (40 тыс. эквивалентных эксплуатационных часов наработки до серьезного ремонта, сравнимого с капитальным);
• возможность проведения ремонта в условиях КС (стационарная турбина);
• высокие показатели надежности (ГТУ SGT-600 хорошо зарекомендовала себя на польских КС газопровода Ямал – Европа).
• современный нагнетатель с высоким политропическим КПД – 85,5%;
• значительная экономия турбинного масла ТП-22 при работе ГПА.
Основой агрегата «Балтика-25» является газовая турбина SGT-600 (прежнее название GT 10В), производимая на предприятии Siemens Industrial Turbomachinery АВ в г.Финспонг, Швеция, и центробежный нагнетатель 12MV2A (производится на заводе Siemens AG в г. Дуйсбург, Германия). ГПА размещается в индивидуальном легкосборном укрытии (металлический каркас с облицовочными панелями типа «сэндвич»), без разделительной стенки между отсеком нагнетателя и газовой турбиной. При проектировании, поставке, сборке и монтаже агрегатов значительную работу выполнило российское отделение корпорации Siemens – ООО «Сименс», а также целый ряд других организаций, имеющих опыт оказания услуг предприятиям ОАО «Газпром», среди них – ЮжНИИГипрогаз, Гипроспецгаз, Стройтрансгаз, СУ-7.
Основные характеристики ГПА «Балтика-25» соответствуют современным требованиям, а по некоторым показателям, таким как выбросы вредных веществ, безвозвратные потери смазочного масла, ГТУ значительно опережает мировые аналоги.
Газовая турбина SGT-600 представляет собой промышленную ГТУ, выполненную по двухвальной схеме с безрегенеративным циклом. Она состоит из 10-ступенчатого компрессора, двухступенчатой ТВД и двухступенчатой свободной силовой турбины. Кроме того, газовая турбина оснащена низкоэмиссионной камерой сгорания кольцевого типа с системой регулируемой подачи «разбавляющего» воздуха и тремя контурами регулирования топливного газа. В системе предусмотрен регулируемый байпас воздуха на выходе камеры сгорания для уменьшения расхода воздуха через горелки на низких режимах.
Двухступенчатый центробежный нагнетатель типа 12MV2A имеет сухие газовые уплотнения тандемной конфигурации с промежуточными лабиринтами (производства компании Burgmann, Германия).
На начало августа текущего года наработка лидерного агрегата на КС «Ухтинская» составила 18,9 тыс. ч, на КС «Вуктыльская» – 17,6 тыс. ч. Суммарная наработка всех шести агрегатов превысила 95 тыс. часов.
Из 27 аварийных остановов, произведенных на шести агрегатах за 4 года эксплуатации, 19 остановов произошли по причине неисправностей агрегатных КИП, 5 – из-за сбоев электрооборудования, вызванных как внутренними, так и внешними причинами, 1 – неисправность в системах маслоснабжения и регулирования (отключение вентилятора АВО воздуха – обледенение проточной части), 1 – по причине механических разрушений деталей (разрушение сухого уплотнения первой ступени нагнетателя) и 1 – по причине попадания инородного предмета (фрагмент ВГУ 70x80) на входную решетку центробежного нагнетателя.
Сервисные подразделения ООО «Сименс» уделяют пристальное внимание эксплуатации агрегатов «Балтика-25» и совместно с ООО «Газпром трансгаз Ухта» делают все необходимое для усовершенствования конструктивных решений, направленных на повышение надежности и эффективности работы агрегатов. Основные моменты этой деятельности и оценки ее заказчиком приведены ниже.
В первый год эксплуатации ГПА выявился ряд вопросов, связанных как с конструктивными особенностями агрегатов, так и с примененными проектными решениями. Так, конструктивные решения системы выхлопа оказались недостаточно проверенными: на всех агрегатах были обнаружены продольные и поперечные трещины на элементах шахт выхлопа (на ГПА в тот момент проводились пусконаладочные работы). Причиной возникновения дефекта стало изменение отработанной конструкции выхлопной системы аналогичных ГТУ, что было связано с недостатком свободной площади на территории КС.
Неоправданным проектным решением, на наш взгляд, является применение для нормальной эксплуатации ГПА (в составе цехового оборудования) системы технологического воздуха, состоящей только из одного воздушного компрессора, ресивера емкостью 4м3 и трубопровода Ду-150. При эксплуатации ГПА выяснилось, что для обеспечения расхода воздуха, необходимого для его подачи одновременно на три агрегата, недостаточно одного компрессора. Кроме того, невозможно резервирование цеховой системы технологического воздуха от работающего газоперекачивающего агрегата с отборами из-за компрессора ГТУ. Аналогичные проектные решения реализованы и на КС «Вуктыльская».
В процессе работы ГПА также отмечены случаи ограничения подачи топливного газа топливным клапаном агрегата, что приводило к последующему снижению частоты вращения силовой турбины до оборотов холостого хода. Отмечались также периодические отключения клапана по причине отключения теплового реле.
В результате анализа опыта эксплуатации агрегатов «Балтика-25» ПО ЭКС ООО «Газпром трансгаз Ухта» совместно с сервисными подразделениями ООО «Сименс» разработали следующий перечень мероприятий, направленных на дальнейшее совершенствование ГПА:
• улучшить систему осушки воздуха собственного отбора;
• настроить алгоритм управления клапана перепуска воздуха системы снижения выбросов;
• добавить возможность ручного управления клапаном противообледенительной системы для осушки фильтров КВОУ при работе ГПА.
Кроме технических задач, следует обратить внимание также и на ряд организационных вопросов. Например, в контракте на поставку газоперекачивающих агрегатов не было предусмотрено постгарантийное обслуживание ГТУ. В поставленный для ООО «Газпром трансгаз Ухта» комплект ЗИП не были включены детали и узлы, имеющие длительный срок изготовления (сухие газодинамические уплотнения и др.).
По этой причине газотурбинные установки находились в вынужденном простое, так как при выходе из строя данных узлов требовалась разовая поставка, что значительно осложнялось отсутствием подписанного с компанией Siemens договора на постгарантийное обслуживание и не позволяло российскому представительству решать вопросы оперативно.
Как считают в ООО «Газпром трансгаз Ухта», при реализации проектов строительства компрессорных цехов с участием зарубежных поставщиков и разработчиков нужно учитывать специфику структуры и организации таких иностранных партнеров. Следует заранее оговаривать разделение границ ответственности между иностранным партнером и его российским представительством, уточнять при покупке нового оборудования не только гарантийные обязательства, но и порядок организации постгарантийного обслуживания.
Нужно своевременно согласовывать перечень запасных частей, необходимых эксплуатирующим организациям, особенно тех узлов и агрегатов, которые имеют длительные сроки изготовления и поставки. Учитывая, что иностранные компании обычно предлагают различные гибкие схемы долгосрочного обслуживания, выбор приемлемой схемы и планирование бюджета для оплаты услуг по таким договорам не представляет особой сложности. А при отсутствии договоров в сложившихся рыночных отношениях эксплуатирующая организация вынуждена самостоятельно решать возникающие вопросы, практически без какой-либо поддержки со стороны иностранной компании, без поставки необходимых дорогостоящих запасных частей, узлов и агрегатов.
Показательным является еще один интересный факт, характеризующий компанию Siemens как надежного партнера. В апреле 2009 года на заводе Siemens в Финспонге был выпущен информационный бюллетень, в котором уведомлялось об отклонениях в лопатках 2-й ступени турбины низкого давления, обнаруженных в некоторых партиях, полученных от субпоставщика в предшествующий период. Такие отклонения были вызваны особенностями литья конкретных партий заготовок, что не влияло на работоспособность лопаток, но ограничивало их ресурс. Часть таких лопаток оказалась установленной в трех из шести ГТУ, уже работавших в тот момент на Ухтинской и Вуктыльской КС.
Система контроля качества Siemens выявила данный факт в ходе инспекции одной из газовых турбин, поставленных на Ближний Восток, и рекомендовала эксплуатирующим организациям, на машинах которых использовались лопатки из данной партии, заменить их в ходе ближайших плановых инспекций. Заботясь об интересах заказчика, ООО «Сименс» согласилось взять на себя замену лопаток на трех газотурбинных установках Ухтинской и Вуктыльской КС. Уже в сентябре того же года новые лопатки были доставлены на площадку. Замена лопаток и балансировка ротора осуществлялась ООО «Сименс» непосредственно на местах эксплуатации ГПА. Две ГТУ на Ухтинской КС уже переоснащены, и еще на одной ГТУ на Вуктыльской КС замена лопаток будет проведена в плановом порядке при ближайшей инспекции.
Любое подведение итогов, даже промежуточных, будет неполным без рассмотрения аспекта экономической эффективности – этому вопросу компания «Газпром» всегда уделяла самое серьезное внимание. И принятие решения по перспективам использования нового газоперекачивающего агрегата сопровождается всесторонним изучением стоимости жизненного цикла. Так, недавно по заказу управления по транспортировке, использованию и хранению газа ОАО «Газпром» специалисты ДОАО «Оргэнергогаз» выполнили оценку стоимости жизненного цикла ГПА «Балтика-25» с учетом стоимости затрат на техническое обслуживание (инспекции А, В, С, Д, Е). В рамках журнальной статьи, конечно, невозможно проиллюстрировать всю многогранность данного исследования, однако на основных результатах стоит остановиться.
Среди главных преимуществ агрегата «Балтика-25», наиболее влияющих на стоимость жизненного цикла, следует назвать следующие:
1. Высокий межрегламентный ресурс;
2. Благодаря гибкой системе исчисления ресурса на базе эквивалентной наработки, ГПА имеет один из самых высоких в своем классе ресурс между капитальными ремонтами. Средняя наработка в эквивалентных часах на 17…20% ниже, чем наработка, зафиксированная в обычных моточасах;
3. Капитальный ремонт, т.е. ремонт ГТУ с заменой деталей горячей части, осуществляется на месте эксплуатации без демонтажа установки;
4. Высокие показатели надежности. Так, анализ опыта эксплуатации примерно 100 агрегатов из почти 300 установленных с начала производства ГТУ SGT-600 показал высокий уровень коэффициента надежности – 99,2% и коэффициента готовности – 97%;
5. Экологические показатели ГТУ SGT-600 обеспечивают минимальный в своем классе мощности уровень эмиссии NOx и СО, что гарантирует серьезную экономию по платежам за выбросы вредных веществ в атмосферу;
6. Рекордно низкие потери масла (менее 70г/ч), что обеспечивает серьезное снижение расходов на ГСМ по сравнению с аналогами.
Совокупность факторов, приведенных в пп. 1-3, несмотря на достаточно высокую стоимость запасных частей, обеспечивает за счет увеличенных интервалов между ТО и ремонтами и отсутствия затрат на транспортировку к месту капремонта настолько низкую стоимость ремонтно-технического обслуживания за весь период эксплуатации, что его доля в полной стоимости жизненного цикла (включая начальные капитальные затраты и стоимость топливного газа) составляет менее 5%.
Таким образом, основной итог анализа экономической эффективности показывает, что стоимость жизненного цикла агрегата «Балтика-25» оказывается на 5…15% ниже, чем в среднем у отечественных аналогов.
Все вышеизложенное позволяет констатировать, что проект локального производства ГПА «Балтика-25» в России отвечает интересам сотрудничества Siemens и Газпрома и способен удовлетворить нужды газотранспортной системы России. Однако вызывает озабоченность тот факт, что, несмотря на постоянный контроль над этим проектом со стороны совместного координационного комитета ОАО «Газпром» и Siemens AG, производство агрегатов на территории России так и не было развернуто. И многие значительные проекты, такие как магистральный газопровод Бованенково – Ухта, так и не получили эту перспективную для своего времени машину. По мнению Департамента по транспортировке, подземному хранению и использованию газа, такой надежный и эффективный агрегат, как «Балтика-25», теряет свою актуальность на фоне появляющихся новых машин различных производителей, предлагающих более высокий КПД и улучшающих показатели ресурсов и надежности. Соответственно, снижается и актуальность проекта в целом.
Тем не менее, говоря о перспективах локализации в России оборудования концерна Siemens AG в интересах газовой отрасли, можно считать позитивным фактором открытие 19 мая этого года совместного предприятия по производству центробежных компрессоров разработки Siemens AG – ООО «РусТурбоМаш».
Хочется надеяться, что новое совместное предприятие станет реальной предпосылкой локального производства оборудования Siemens в России, позволит сдвинуть проект «Балтика-25» с мертвой точки. По словам сопредседателя подгруппы «Компрессорные станции» Ральфа Каннефасса на 17-м заседании координационного комитета по сотрудничеству между ОАО «Газпром» и Siemens AG, концерн Siemens намерен самым непосредственным образом включить новое предприятие в кооперацию по производству ГПА «Балтика-25».
Таким образом, можно смело утверждать, что агрегат «Балтика-25» доказал свою надежность, высокую эффективность и экологичность и что сотрудничество компании Siemens с Газпромом и другими российскими партнерами может удовлетворить самые амбициозные планы ОАО «Газпром», обеспечив его в ближайшие несколько лет надежной техникой российского производства. 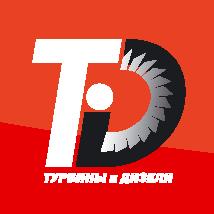