Т.У. Магометбеков, А.Л. Сабуров – ООО «Сименс»
К.В. Камышинный – ООО «Энерготех» (Москва)
Применение газотурбинных установок на Хасырейском нефтяном месторождении обеспечило автономное энергоснабжение группы месторождений Вала Гамбурцева с использованием в качестве топлива попутного нефтяного газа с высоким содержанием серы.
Хасырейское нефтяное месторождение, наравне с Черпаюским и Надейюским, входит в группу месторождений Вала Гамбурцева (Ненецкий автономный округ), суммарные геологические запасы которого оцениваются в 192 млн тонн, а извлекаемые – в 65 млн т. Тендер на право разработки нефтяного пласта Вала Гамбурцева в 2001 году выиграла компания «Северная нефть». Хасырейское является одним из наиболее удаленных месторождений, принадлежащих ООО «РН-Северная нефть». Оно находится более чем в 300 км от ближайших населенных пунктов, линий электропередачи, транспортных магистралей и существующих промыслов.
Было принято решение о строительстве мощного автономного энергоцентра, работающего на попутном нефтяном газе (ПНГ), который обеспечит электрической энергией технологические и жилые объекты нефтяного промысла. Для этого существовал ряд предпосылок:
• удаленность месторождений Вала Гамбурцева от линий электропередачи;
• большое количество ПНГ в составе извлекаемой нефти;
• возросшие штрафы за сжигание ПНГ в связи с ратификацией Киотского протокола, согласно которому нужно было сократить выбросы углекислого газа;
• необходимость энергообеспечения близлежащих месторождений – Черпаюского и Надейюского, разрабатываемых компанией «Северная нефть».
В связи с тем, что химический анализ показал в составе ПНГ большое количество сероводорода (около 3%), формирование энергоцентра на базе газопоршневых энергоблоков было невозможно. Компанией «Северная нефть» был отправлен запрос ведущим производителям энергетического оборудования на базе газотурбинных двигателей с требованиями, согласно которым производитель гарантировал бы устойчивую работу на попутном нефтяном газе с содержанием сероводорода 3%. Компания Siemens Industrial Turbomachinery, Ltd (Великобритания) представила гарантии и подтверждение работоспособности своего оборудования на топливе этого состава.
Поставщиком газотурбинного оборудования выступила фирма «Энерготех» (Москва), которая выполняла также шефмонтажные и пусконаладочные работы.
Строительство энергоцентра согласно условиям контракта осуществляется в три этапа и должно быть реализовано до конца 2007 года. Общая мощность энергоцентра к этому времени составит 33 МВт. На первом этапе были введены в эксплуатацию два газотурбинных агрегата Siemens SGT-100 (Typhoon) единичной мощностью 4,7 МВт, работающих на ПНГ. Пусконаладочные работы были закончены весной 2004 года, и в настоящий момент обе газотурбинные установки обеспечивают месторождение электроэнергией.
На втором этапе в состав энергоцентра должны быть введены два агрегата Siemens SGT-300 (Tempest) единичной мощностью 7,9 МВт. Первая ГТУ введена в эксплуатацию в сентябре, запуск второй установки планируется в январе 2007 года – в настоящее время ведутся пусконаладочные работы.
Генеральным проектировщиком строительства выступило ООО «ИЛФ Русланд, Инжиниринг и Проектное управление» – российское представительство компании ILF Consalting Engineers (Австрия-Германия). Основные строительные работы осуществляло одно из ведущих региональных предприятий промышленного строительства – ООО «Строймонтаж» (г. Усинск).
В состав электростанции входят четыре функционально взаимосвязанных легковозводимых сооружения. Они расположены на технологических площадках на высоте 1,5 м от земли. Площадки укреплены на сваях, которые вбиты на глубину 12…18 м (до твердых пород).
Архитектурное решение электростанции включает в себя главный корпус ГТЭ, пункты подготовки топливного газа и технологического воздуха, резервуар для хранения масла. В главном корпусе размещены газотурбинные установки, вспомогательное и электротехническое оборудование, а также аппаратура КИП и АСУ ТП. Все отделения главного корпуса подведены под общую кровлю. Причем, площадь машинного зала наращивалась по мере монтажа нового оборудования, а внешняя стена после возведения пристройки служила внутренней перегородкой между отдельными агрегатами для улучшения звукоизоляции.
Интересным решением также можно назвать эффективное использование пространства между землей и технологической площадкой. Лотки, укрепленные на сваях ниже уровня площадки, служат опорами для линий инженерных систем ГТУ.
В каждом машинном зале размещено по два энергоблока и одной щитовой, в которой находится силовое электротехническое оборудование и различные системы для обеих установок.
Газотурбинный энергоблок
Газотурбинные двигатели SGT-100 и SGT-300 унифицированы: так, SGT-300 является увеличенной аэродинамической версией своего предшественника. Конструкции энергоблоков аналогичны, поэтому в статье дано описание двигателя SGT-300, как более современного и экономичного.
SGT-300 – одновальный промышленный газотурбинный двигатель открытого цикла, с приводом на стороне компрессора. Объединение новейших технологий, конструкций и материалов позволило создать промышленный двигатель с характеристиками, близкими к характеристикам авиапроизводной ГТУ, но сохранив при этом преимущества агрегата промышленного типа. Компрессор – осевой, околозвуковой, 10-ступенчатый. Кожух компрессора является разъемным – это сводит к минимуму время демонтажа и облегчает инспектирование компонентов. Ротор – дискового типа, диски имеют хертовое соединение и стянуты центральным болтом. Первые 4 ступени имеют передовую аэродинамическую конструкцию с короткой хордой. Лопатки ротора крепятся к дискам при помощи хвостовиков типа «ласточкин хвост».
Четыре ряда направляющих аппаратов – регулируемые, что обеспечивает максимальный КПД компрессора и его надежную работу на различных режимах. Привод лопаток – гидравлический, в качестве рабочего тела используется смазочное масло. Стандартная конструкция кожуха воздухозаборника предусматривает его вертикальное расположение. Для дополнительной защиты от проникновения посторонних предметов он снабжен решеткой. На фланце кожуха воздухозаборника для компенсации температурных расширений установлен компенсатор из неопренового резиноподобного полимера с тонкой хлопковой вставкой.
Камера сгорания – осевая, трубчатого типа, состоит из шести жаровых труб, имеющих двустенную конструкцию. Они снабжены системой горелок для подготовки обедненной топливной смеси, что позволяет снизить температуру пламени и, соответственно, уровень выбросов оксидов азота. Функцию зажигания выполняет пилотная горелка, расположенная в головке жаровой трубы. Компоненты камеры сгорания изготовлены из сплава Haynes 230, конструкция их крепления допускает свободное температурное расширение, обеспечивая минимизацию температурных напряжений и увеличение срока службы. Розжиг осуществляется с помощью искровых электродов (по одному на каждую жаровую трубу).
Турбина – осевая, околозвуковая, 2-ступенчатая. Охлаждаемые рабочие колеса первой ступени изготовлены из сплава INCO 6203DS. Лопатки второй ступени – неохлаждаемые, выполнены из сплава Udimet 720. Сопловые аппараты, изготовленные из сплава IN-939, имеют диэдральную конструкцию. Первая ступень имеет конвекционно-пленочное охлаждение, вторая – неохлаждаемая. Для компенсации движений, вызванных температурным расширением, на диффузоре выхлопных газов турбины установлен высокотемпературный компенсатор.
На щит управления турбины поступает информация о рабочей температуре двигателя от датчиков температуры, расположенных в кожухе воздухозаборника, и от термопар, находящихся на выходе силовой турбины. Для контроля условий сгорания топлива используются термопары на выходе турбины, которые отключают двигатель, в случае если в одной из жаровых труб погаснет пламя.
Каждый подшипник двигателя снабжен двумя встроенными термопарами (активная и резервная) для контроля температуры. Скорость вращения вала контролируется датчиком скорости. Уровни вибрации в двигателе измеряются с помощью бесконтактной системы. На упорных подшипниках закреплены датчики, работающие в плоскостях X-Y (активный и резервный). Каждый упорный подшипник вала снабжен датчиком, работающим в плоскости Z.
Единая рама энергоблока, изготовленная из малоуглеродистой стали, включает встроенный бак смазочного масла. На ней размещено также вспомогательное оборудование. Двигатель и редуктор опираются на торсионное кольцо, которое жестко закреплено на плите основания.
Система смазочного масла обеспечивает маслом (ISO VG 46) двигатель, редуктор и генератор. Бак изготовлен из низкоуглеродистой стали, его рабочий объем 1408 литров. Величина безвозвратных потерь смазочного масла указана в таблице. Большая их часть обусловлена потерями в системе суфлирования бака смазочного масла.
Основной масляный насос – шестеренчатого типа. Он работает от механического привода главного редуктора. Масло предварительной и последующей смазки подается насосом с приводом от 2-полюсного электродвигателя переменного тока. На случай отключения от сети переменного тока агрегат оборудован аварийным насосом, запитываемым от сети постоянного тока, который подает масло для обеспечения выбега двигателя. Аккумуляторные батареи для питания насоса установлены в помещении щитовой – их мощности достаточно для электропитания в течение трех часов.
Контроль за температурой смазочного масла осуществляется с помощью термостатического клапана. При нормальных эксплуатационных условиях температура масла, подаваемого в турбину, составляет 60 °С. Давление масла на подшипнике турбины регулируется также при помощи клапана. Тонкость фильтрации подаваемого в двигатель масла составляет 10 мкм – для этого применяется фильтр дуплексного типа.
Охладитель смазочного масла – радиаторного типа, с высокой скоростью обдува – изготовлен фирмой Alfa Laval. Охлаждающий двухскоростной вентилятор имеет привод от электромотора переменного тока.
Для уменьшения засорения компрессора и удаления накопившихся отложений служит система промывки. Она включает всю трубную обвязку с разбрызгивающими соплами, размещенную в кожухе воздухозаборника турбины.
Пусковой двигатель мощностью 90 кВт (переменного тока, с регулируемой скоростью) соединен с главным редуктором посредством муфты сцепления SSS.
Газовая топливная система имеет всю необходимую трубную обвязку. Она установлена на раме основания двигателя вместе со всем оборудованием, необходимым для управления подачей. Температура газа на входе в топливную систему должна быть не более 105 °С, но выше точки росы ПНГ не менее чем на 20 °С. Топливо поступает в турбину через два пожаробезопасных шаровых крана, которые обеспечивают возможность отсечения топливной системы от трубопроводов подачи газа.
Воздушный фильтр воздухозаборника поставлен компаниями Altair Ltd и Clarcor UK Ltd (Великобритания). Он имеет систему периодической импульсной очистки сжатым воздухом в обратном направлении, удаляющую наслоения пыли с поверхности фильтра. Подогреватели циклового воздуха включаются при температуре на входе минус 37 °С.
Глушитель, устанавливаемый на линии забора воздуха, выполнен из нержавеющей стали и служит для снижения шума – общий уровень звукового давления не должен превышать 85 дБ(А). Глушитель отработавших газов также изготовлен из нержавеющей стали.
Автономный понижающий редуктор фирмы Allen Gears – планетарный. Частота вращения на выходе турбины составляет 14010 об/мин, а на выходе редуктора – 1500 об/мин. Между редуктором и генератором установлена гибкая муфта. Ограничение крутящего момента достигается за счет срезного штифта. Устройство срабатывает при превышении номинального рабочего крутящего момента в 2,25 раза.
Автоматический регулятор напряжения включает ограничитель напряжения/частоты, ограничитель перевозбуждения/недостаточного возбуждения.
Звукоизолирующий кожух закрывает двигатель и редуктор. Кожух крепится к плите основания, на которую для снижения шума уложен 18-мм трехслойный лист с мягким неопреновым слоем в середине. Обшивка боковых панелей изготовлена из негорючего, негигроскопичного, звукопоглощающего материала, закрепленного на внутренней стороне панелей при помощи перфорированных стальных листов. Для эффективного поглощения шума и предотвращения попадания пыли внутрь стыки выполнены герметичными. Дверцы размещены в местах, обеспечивающих доступ к горелкам и фильтрам.
В конструкции предусмотрена подъемная балка для снятия верхней половины двигателя и основания редуктора. Система воздушной вентиляции кожуха имеет глушители, изготовленные из нержавеющей стали, которые располагаются на входе и выходе системы. Кожух оборудован углекислотной системой пожаротушения двухкратного действия, состоящей из 2 комплектов спаренных 45-килограммовых баллонов с СО2, которые размещаются в машинном зале вблизи турбоагрегата.
Синхронный генератор Alstom Power Conversion Ltd. «Альфа» – четырехполюсный, с частотой вращения 1500 об/мин. Система смазки генератора – принудительная. Сердечник статора, с ламинированной обмоткой и радиальными вентиляционными каналами, установлен в коробчатой раме. Ротор – явнополюсного типа, с ламинированным сердечником. Подвесной возбудитель, в комплекте с постоянным магнитным генератором (ПМГ) на валу, монтируется на выступе коробчатой рамы. Для возбудителя и ПМГ охлаждающий воздух подается из главного кожуха машины через каналы в выступе. Внешнее охлаждение с первичным теплоносителем (воздух), изолированным от окружающего воздуха и циркулирующим внутри машины, осуществляется за счет установленных на валу вентиляторов. Вторичный теплоноситель (воздух) направляется через теплообменник при помощи вентиляторов с приводом от независимых электродвигателей.
Управление энергоблоком
Шкаф управления энергоблоком размещается в помещении щитовой. Отдельный компьютер используется для отображения информации и для управления системой. Системы пожаро-и газообнаружения, а также контроля вибрации встроены в САУ двигателя. В системе управления используется ПЛК Allen-Bradley Control-LogixTM, который осуществляет защиты двигателя, мониторинг сбоев, оповещение, контроль расхода топлива и скорости вращения двигателя, мониторинг температурного режима.
На экран выводятся цифровые показатели, для наглядности информация представляется также в виде графиков и диаграмм. Выводимые на дисплей данные о текущем состоянии двигателя дают оператору свежую информацию о параметрах работы компрессора, камеры сгорания, турбины. Дисплей ведомого узла отображает информацию о генераторе. Выведение на дисплей вспомогательной картины дает информацию о топливной системе и уровнях вибрации.
Различные мнемосхемы отображают положение регулируемого направляющего аппарата и углы открытия топливного клапана, показания термопары «газового тракта», сведения о температуре подшипников, температуре и давлении в системе смазки и др.
Интерфейс «человек-машина» состоит из схемно-реализованных нажимных кнопок и 15-дюймового ЖК сенсорного экрана. Дисплей выводит текстовые сигналы тревоги и сообщения о срабатываниях (отключениях), соответственно, желтого и красного цвета, с индикатором подтверждения и дополнительными информационными сообщениями. Всплывающее, управляемое событиями окно показывает последние четыре сообщения. Это окно также играет роль хранителя экрана, когда дисплей некоторое время не используется.
В файле истории сохраняется до 100 сообщений с метками времени и даты. Доступен вариант мнемосхемы с трендами регистрируемых данных, позволяющий одновременно выводить до восьми аналоговых и двух цифровых кривых. Они могут представить любой введенный параметр в процентном отношении от максимума за период, определяемый в сутках, часах, минутах или секундах.
АСУ ТП электростанции
Система управления станции выполнена на элементной базе компании Allen Bradley. Верхний уровень обеспечивает реализацию функций отображения информации на АРМ операторов, дистанционного контроля и управления технологическим процессом, настройки компонентов системы, протоколирования и архивирования данных. Элементы верхнего уровня АСУ обеспечивают следующие функции:
• выдачу информации о технологическом процессе на АРМ операторов;
• обмен информацией с аппаратно-программным комплексом нижнего уровня;
• архивирование входящей и исходящей информации;
• возможность формирования и передачи пакетов данных в АСУ вышестоящего уровня в соответствии с принятыми в указанном уровне стандартами.
Нижний уровень обеспечивает выполнение функций сбора, преобразования, первичной обработки входных сигналов от датчиков, исполнительных и контрольных устройств, а также автоматическое управление, регулирование, защиту и блокировки передачи данных на верхний уровень АСУ в пределах заложенных программно-аппаратных возможностей.
Оборудование системы управления выполнено с применением современных полевых и локальных контроллеров, аппаратно конфигурируемых по блочному принципу, при минимальном количестве функциональных плат. Питание средств системы управления осуществляется от 24 В постоянного тока и 220 В переменного тока от сети гарантированного электроснабжения.
Средства АСУ обеспечивают ручное, полуавтоматическое и автоматическое управление и контроль параметров оборудования энергоцентра. Оборудование АСУ работает при температуре окружающего воздуха до +60 °С. Система управления строится по принципу аппаратного масштабирования для дальнейшего расширения, модернизации, развития системы.
Система управления электростанции размещена на первом этаже здания в объединенном помещении операторной и электрощитовой энергоцеха №1 (два энергоблока SGT-100).
Система подготовки топливного газа
Система включает фильтры грубой очистки, компрессорный блок (3 компрессорных агрегата Ariel), ресивер топливного газа (для исключения колебаний давления газа при включении/выключении ГТУ), систему очистки и осушки газа.
Компрессорный агрегат (3 шт.) выполнен на базе двуступенчатых поршневых компрессоров Ariel JGK/2. Производительность электроприводного компрессора 160000 м3/сут, давление на всасывании 0,4 МПа, на нагнетании – 2,58 МПа. Температура нагнетания второй ступени 118 °С, мощность на валу – 560 кВт. Фильтрационные модули – сепараторного типа (российского производства). Система сероочистки не применялась, так как компания Siemens подтвердила устойчивую работу установок на ПНГ такого состава.
Подготовка технологического воздуха
Система предназначена для обеспечения работы пневматических систем автоматики ГТУ. На каждую турбину – одна компрессорная станция (КС) производительностью 5,2 м3/мин. Она размещается в компрессорной технологического воздуха, которая состоит из двух (основная и резервная) винтовых установок «Шторм 0600» производства ООО «Борец» (Москва). Компрессорная находится в отдельном здании, где расположены все КС. Максимальная единичная потребляемая мощность – 66 кВт. Рабочее давление 0,5...1 МПа.
Установки предназначены для эксплуатации в условиях умеренно холодного климата (УХЛ4) – при относительной влажности воздуха до 80% при +25 °С. Гарантируется работа оборудования станции в диапазоне температур –40...+40 °С. Для поддержания в здании температуры выше +5 °С используется тепловая завеса.
Реализация проекта
На третьем этапе строительства ООО «Энерготех» обеспечит ввод в эксплуатацию еще одного агрегата SGT-300. Он будет снабжен модулем жидкого топлива, обеспечивающим двухтопливный режим работы ГТУ на ПНГ и дизельном топливе. Это решение принято в связи с нестабильностью состава и количества ПНГ на месторождении и с целью повышения надежности энергообеспечения.
Энергоустановка изготавливается на заводе Siemens в г. Линкольн, срок отгрузки – февраль 2007 года. ГТУ по зимнику будет доставлена на станцию, ввод ее в эксплуатацию планируется осенью следующего года. 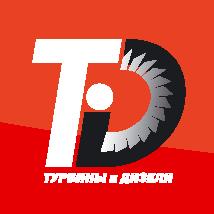