И.В. Сушков – ОАО «Доминанта-Энерджи»
В феврале состоялся торжественный пуск первой очереди комплекса по генерации электроэнергии на Ван-Еганском месторождении нефти (Тюменская область, ХМАО – Югра). Он представляет собой многоагрегатную газотурбинную электростанцию установленной мощностью 36,26 МВт. Комплекс спроектирован компанией «Доминанта-Энерджи» по заказу СП «Ваньеганнефть».
Газотурбинная электростанция расположена на площадке центрального пункта сбора нефти (ЦПС) Ван-Еганского месторождения, вблизи г. Радужный, (Тюменская обл.). Заказчиком проекта выступает СП «Ваньеганнефть» (ТНК), г. Нижневартовск.
Генеральный проектировщик – ОАО «Доминанта-Энерджи» (С.-Петербург). В соответствии с условиями договора компания разработала и согласовала проектную документацию в органах госэкспертизы и с заказчиком – ТНК-ВР, осуществила поставку и монтаж газотурбинных установок, часть работ по строительству, обеспечила авторский надзор за строительством. В присутствии заказчика произведен пуск первой очереди электростанции в составе двух энергоблоков.
ГТЭС построена на основе семи газотурбинных электроагрегатов СХ501-КВ7 производства компании Centrax Ltd. (Великобритания). ГТУ созданы на базе газотурбинных двигателей Rolls-Royce. Режим работы электростанции – базовый. Постоянная выработка электроэнергии для нужд потребителей Ван-Еганского месторождения осуществляется шестью агрегатами, седьмой – в резерве. Установленная электрическая мощность ГТЭС составляет 36,26 МВт. Электроэнергия напряжением 6,3 и 35 кВ подается через повышающую подстанцию ПС 6/35 кВ, также построенную по разработанному проекту.
Газотурбинные электроагрегаты СХ501-КВ7 модульного исполнения установлены в помещении машинного зала производственного корпуса. Здание производственного корпуса состоит из трех блоков: машинный зал размерами в осях 18x48 м, высотой до низа ферм покрытия 10,5 м и две одноэтажные пристройки. В одной из них (3,1x9,05 м) располагается маслохозяйство, в другой (27,0x15,5 м) – распределительные устройства РУ 6,3 кВ и РУ 0,4 кВ, тепловой пункт, блок водоподготовки, склад гипохлорита натрия.
Производственный корпус представляет собой быстровозводимое здание из готовых металлических конструкций высокой заводской готовности. Площадь застройки составляет 1431,6 м2, полезная площадь – 1331,3 м2. Стены и покрытия кровли изготовлены из сэндвич-панелей толщиной 150 мм и 200 мм соответственно. Здание корпуса имеет водяное и электрическое отопление, приточно-вытяжную механическую вентиляцию, водоснабжение, естественное и электрическое освещение. Помещения для персонала станции (административно-бытовой блок, операторная, мастерская и кладовая ЗИП, контрольно-пропускной пункт) выполнены в виде отдельно стоящих блоков полной заводской готовности. Основания всех объектов в соответствии с геологическими условиями расположения площадки – свайные.
Газотурбинные электроагрегаты единичной мощностью 5,18 МВт смонтированы в звукоизолированных утепленных контейнерах. Модульная конструкция обеспечивает удобство монтажа и проведения пусконаладочных работ. Перед отправкой на объект электроагрегаты прошли стендовые испытания на предприятии-изготовителе.
Энергоблоки работают в параллель между собой и с энергосистемой ОАО «Черногорэнерго». Топливом является подготовленный попутный нефтяной газ, для чего на территории электростанции смонтирована установка подготовки топливного газа (УПТГ).
В качестве привода в Centrax СХ501-КВ7 используется газовая турбина Allison 501-КВ7. Наряду с высокими показателями надежности, подтвержденными длительной эксплуатацией двигателей серии 501 (выпускается с 1963 г., более 18 тыс. двигателей, суммарная наработка более 200 млн часов), агрегат имеет высокие показатели эффективности и низкие эксплуатационные расходы. Благодаря высокой надежности, незначительному регламентному обслуживанию и длительному интервалу между капитальными ремонтами (более 35 тыс. часов) двигатель хорошо подходит для использования его в качестве привода электрогенераторов. На сегодня в промышленной эксплуатации находится более 2500 газотурбинных двигателей 501-КВ7. По заявлению компании Centrax, наработка некоторых агрегатов данной серии превысила 180 тыс. часов.
Двигатель 501-КВ7 – одновальной конструкции. Компрессор – осевой, 15-ступенчатый, πк=13,5, с нулевой центробежной бустерной ступенью. Ротор смонтирован на одном стяжном валу. Статор включает направляющие аппараты ступеней компрессора и имеет истираемые концевые уплотнения.
Камера сгорания – трубчато-кольцевая, прямоточная, шесть жаровых труб размещены радиально, в каждой трубе размещено по одной топливной форсунке. Розжиг в камере сгорания при пуске происходит от двух искровых разрядов в свечах зажигания, расположенных в двух диаметрально противоположных жаровых трубах. Распространение пламени по камере сгорания достигается за счет использования переходных труб, которые также обеспечивают баланс горения.
Горячие газы из камеры сгорания под высоким давлением попадают в 4-ступенчатую осевую турбину, где, расширяясь, обеспечивают выработку механической энергии. Рабочие лопатки и лопатки соплового аппарата первой ступени – охлаждаемые. Вал отбора мощности расположен с холодной стороны установки, в связи с чем термические расширения не оказывают негативного воздействия.
СХ501-КВ7 является одним из самых компактных и эффективных приводных двигателей – его КПД может достигать 31,5% при работе на номинальном режиме (согласно ISO). Привод имеет низкий вес – менее 1 тонны, что обеспечивает его доставку авиатранспортом в любую точку мира.
В ГТУ применен генератор LSA56BUL85 производства Leroy-Somer (Франция). Двигатель и генератор закреплены на одной раме. Генератор переменного тока напряжением 6,3 кВ представляет собой бесщеточную самовентилирующуюся электрическую машину с вращающимся полем, явновыраженными полюсами. Имеет автоматическое регулирование напряжения и коэффициента мощности. На валу генератора смонтирован узел вращающихся диодов и вентиляторы. Генератор выбран с запасом по номинальной мощности, превышающей мощность газотурбинного двигателя для всех условий эксплуатации.
Ротор генератора переменного тока опирается на два масляных подшипника скольжения. Масло подается в подшипники под давлением со стороны турбины от главного масляного насоса редуктора. Система смазки – единая для двигателя, редуктора и генератора. Генератор выдерживает 10%-е перегрузки в течение 1 часа с шестичасовым интервалом.
Система управления электроагрегатом скомпонована в односекционной панели, установленной в торце контейнера ГТУ с холодной стороны двигателя. Параметры работы ГТУ контролируются посредством серии программируемых логических контроллеров (PLCs) и блока управления двигателем. PLCs-управление выполняется через удаленные модули ввода/вывода, которые соединяются с использованием сети Siemens Profibus.
Компьютер SCADA Centrax (supervisory cotrol and data acquisition – диспетчерское управление и сбор данных) может использоваться при необходимости для управления ГТУ из удаленного места. Имеется резервное электрическое питание системы управления от аккумуляторной батареи постоянного тока 24 В.
Установка подготовки топливного газа. Для подготовки попутного нефтяного газа до требуемых со стороны изготовителя ГТУ параметров в составе комплекса применяется установка подготовки топливного газа. УПТГ изготовлена московской фирмой «НОЭМИ». Она представляет собой комплекс из четырех блоков компримирования газа и общестанционного оборудования, к которому относятся два ресивера газа высокого давления объемом 16 м3 и модуль концевого оборудования. Для предварительной очистки газа в составе установки используются газовые сепараторы ГС 2 ОСТ 26-02-2059-79 объемом 8 м3.
Для нормальной работы ГТУ требуется топливный газ давлением не выше 2,0 МПа (изб.) и не ниже 1,7 МПа, температура газа не должна превышать 82 °С и не опускаться менее, чем на 10 °С выше температуры точки росы. Очень важной характеристикой состава газа является отсутствие в нем всех капель жидкости и твердых частиц (размером 1 мкм – 99%, более 3 мкм – 99,5%). В составе УПТГ применены компрессоры TT-T48S-28 Grasso с электроприводом 630 кВт от двигателя M3JP/KP400LKB (3000 об/мин, 0,4 кВ) производства компании ABB.
Воздушная компрессорная станция. Для работы запорно-регулирующей арматуры, системы импульсной очистки воздушных фильтров и системы промывки ГТУ требуется сжатый воздух. В состав энергокомплекса входит модульная воздушная компрессорная станция. Она обеспечивает требуемую номинальную производительность 21 м3/ч и максимальную (для системы импульсной очистки) – 200 м3/ч, давление нагнетания макс. 0,8 МПа (изб.), мин. – 0,7 МПа (изб.). Качество сжатого воздуха соответствует ISO 8573.1-3-1-3 (точка росы минус 70 °С). Компрессорная станция изготовлена компанией «Далгакыран Северо-Запад» (С.-Петербург).
Система выхлопа (СВ) предназначена для отвода выхлопных газов и снижения шума струи выхлопных газов, снижения температуры газов перед выходом в атмосферу. В связи с тем что проектом не предусмотрена система утилизации тепла выхлопных газов, СВ соединена с выхлопным фланцем ГТУ напрямую через компенсатор линейных расширений.
В составе СВ применен шумоглушитель, обеспечивающий уровень шума не более 80 дБ(А) на расстоянии 1 м по горизонтали и 1,5 м по высоте от основания СВ. Аэродинамическое сопротивление выхлопного тракта системы выхлопа не превышает 650 Па.
СВ изготовлена Ухтинским экспериментально-механическим заводом, который имеет многолетний опыт работы в области производства систем выхлопа и шумоглушения для ГТД различной размерности. На площадку электростанции система выхлопа поставлена укрупненными транспортными блоками.
Система вентиляции машинного зала и ГТУ. Система вентиляции машинного зала включает в себя приточные воздушные установки технологической вентиляции ГТУ, а также помещений машинного зала.
Технологическая вентиляция газотурбинной установки предназначена для подачи воздуха для вентиляции контейнера и для горения в ГТУ. Забор воздуха осуществляется с улицы с помощью воздуховода вентиляции ГТУ и воздуховода подачи воздуха на горение. В случае когда наружная температура ниже 10 °С, к воздуху, поступающему с улицы, в воздуховоде вентиляции ГТУ подмешивается подогретый с помощью маслорадиатора установки воздух из машзала.
Прошедший через контейнер воздух выбрасывается сразу в атмосферу через кровельные дефлекторы. Таким образом, в ГТУ поступает воздух требуемой температуры, а в машинном зале обеспечивается постоянная смена воздуха за счет работы приточных вентиляционных установок и потребления воздуха вентиляции турбиной.
Воздух, поступающий в машинный зал, подогревается за счет работы приточных установок. Кроме того, в машзале имеется система водяного отопления, запитываемая от теплового пункта. Тепло поступает с расположенной рядом котельной ЦПС Ван-Еганского месторождения.
Система управления и контроля ГТЭС. Система управления и контроля (АСУ ТП) предназначена для надежной эксплуатации основного и вспомогательного оборудования систем ГТЭС в ручном и автоматизированном режиме.
Система выполнена в виде пяти связанных между собой подсистем – автоматизированные системы управления турбинами (АСУ Т), вспомогательными системами (АСУ ВС), электрическими системами (АСУ Э); система автоматического пожаротушения и сигнализации; система управления ВКУ. Каждая подсистема получает информацию о состоянии оборудования и передает на шкафы управления систем и на автоматизированные рабочие места (АРМ) операторов подсистем. Таким образом, управление может осуществляться как непосредственно со шкафов, так и с АРМ.
Предусмотрены два АРМ – инженера-технолога и инженера-электротехника. АРМ расположены в операторной, шкафы управления – в производственном корпусе. На АРМ технолога поступает информация от ВКУ, УПТГ и других вспомогательных систем, на АРМ электротехника – о состоянии выключателей РУ 6,3 кВ и РУ 0,4 кВ, а также информация от локальных панелей управления ГТУ. Система автоматического контроля загазованности, пожаротушения, охранно-пожарной сигнализации позволяет автоматически прекращать работу ГТУ, ВКУ, управлять вентиляцией, отключать необходимые выключатели.
Предусмотрена возможность подключения системы управления верхнего уровня – всем энергокомплексом в целом (АСУ П). Контроль и ручное управление осуществляется через главный щит управления ГТЭС.
Первый пуск показал надежную работу всех систем, ГТУ, электрооборудования. В настоящий момент проводится отладка системы газоподготовки в части очистки попутного нефтяного газа от конденсата.
Ввод всех ГТУ в составе энергокомплекса на номинальную мощность запланирован до конца текущего года. ОАО «Доминанта-Энерджи» успешно осуществляет авторское сопровождение энергетического объекта в эксплуатации, включая сервисную поддержку поставленного оборудования. 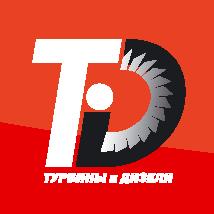