Е.А. Захаренков, В.Д. Буров – Московский энергетический институт (Технический университет)
Технологии на основе топливных элементов – перспективное направление малой энергетики в настоящих условиях. Экологически чистое и эффективное производство электроэнергии привлекает все больше разработчиков и производителей в эту область энергетики.
Типы топливных элементов и принцип их работы
Топливные элементы (ТЭ) являются электрохимическими устройствами, которые преобразуют химическую энергию топлива в электрическую и тепловую энергию, и происходит это эффективнее, чем в обычных технологиях со сжиганием. ТЭ представляют собой «неистощимые батарейки», к которым непрерывно подводится топливо и воздух.
В зависимости от примененного электролита можно выделить следующие основные типы топливных элементов [1]:
• фосфорнокислые (ФКТЭ). Их КПД при выработке электроэнергии составляет около 40%, при совместном производстве тепла и электричества – около 80%. Рабочие температуры находятся в пределах 180...230 °С. ТЭ на фосфорной кислоте имеют относительно невысокий КПД и требуют некоторого времени для выхода на рабочий режим при холодном старте. Но при этом они отличаются довольно простой конструкцией, высокой стабильностью и низкой летучестью электролита. На базе этих элементов созданы энергоустановки мощностью от 200 кВт до 20 МВт.
• твердополимерные (ТПТЭ). Эти топливные элементы отличаются компактностью, высокой степенью надежности и экологической безопасности. КПД твердополимерных топливных элементов составляет около 45%, рабочая температура – около 80 °С. В качестве топлива используется чистый водород. Серьезным препятствием на пути широкого распространения этих топливных элементов является высокая стоимость получаемой с их помощью электроэнергии (в ТПТЭ применяются катализаторы из платины и ее сплавов). Тем не менее, обладая уникальными качествами, они имеют хорошую перспективу для широкого применения.
• ТЭ на расплавленном карбонате (РКТЭ). Данный тип относится к высокотемпературным устройствам. Высокая рабочая температура ТЭ (600...700 °С) позволяет использовать в качестве топлива природный газ, который преобразуется встроенным конвертером в водород и монооксид углерода. КПД достигает 55%. В связи с большим количеством выделяемого при работе тепла, РКТЭ успешно применяются для создания стационарных источников электрической и тепловой энергии.
• твердооксидные (ТОТЭ). В этих топливных элементах вместо жидкого электролита применяется твердый керамический материал, что позволяет достигать высоких рабочих температур – 900...1000 °С. КПД составляет около 50%. ТОТЭ могут работать на различных видах углеводородного топлива без преобразования его в водород. Топливные элементы с твердым электролитом имеют хорошую перспективу для использования в промышленных установках большой мощности.
Поскольку топливные элементы сделаны из разных материалов и имеют разную температуру, у каждого типа ТЭ своя область применения, свои особенности и преимущества, но всех их отличает большой потенциал эффективности и низкого экологического воздействия. Топливные элементы, работающие при относительно низких температурах, производят незначительное количество NOx. Оксиды серы (SOx) также отсутствуют, так как топливо для ТЭ предварительно от нее очищается (попадание серы в топливные элементы недопустимо) [2].
В топливных элементах вместо горения происходят электрохимические реакции, поэтому им необходимо легкоокисляемое вещество, такое как водород. Некоторые высокотемпературные топливные элементы, например ТОТЭ и РКТЭ, могут также использовать монооксид углерода (СО). Это делает их более гибкими к топливу и более эффективными за счет применения доступных видов топлива, таких как природный газ и пропан. Водород и СО можно получить из природного газа и других видов топлива, например, посредством паровой конверсии.
Топливные элементы типа ТОТЭ и РКТЭ, которые могут преобразовывать природный газ внутри ТЭ, имеют значительные преимущества при его использовании, так как не требуется дополнительных внешних конвертеров. Кроме того, при внутренней конверсии преобразуется почти весь природный газ в водород и СО, а эффективность внешних конвертеров – только до 80% [3].
В основе принципа работы топливного элемента – перемещение ионов через электролит при подаче воздуха и топлива в ТЭ. В твердооксидных топливных элементах воздух ионизируется на катоде, и ионы кислорода протекают через электролит. Достигнув топлива у анода, они окисляют водород до Н2О и СО до СО2. В процессе этих реакций электроны освобождаются, и, если анод и катод соединены с внешней цепью, поток электронов становится постоянным током. Этот процесс продолжается до тех пор, пока топливо и воздух подводятся к элементу. Принцип действия других типов топливных элементов аналогичен, но каждый из них имеет свои особенности.
Электрохимические установки
Хотя процесс превращения химической энергии в электрическую осуществляется непосредственно в ТЭ, одного элемента недостаточно для непрерывной генерации электроэнергии. Поскольку напряжение и ток единичного топливного элемента невелики, для получения заданных характеристик топливные элементы соединяют в батареи. Для постоянного получения электроэнергии необходимо в батарею ТЭ непрерывно подводить окислитель и топливо, выводить из нее продукты реакции, поддерживать постоянную температуру, регулировать напряжение и т. д.
Электрохимическая установка (ЭУ) на основе твердооксидных топливных элементов [2] имеет встроенный реформер для конверсии высших углеводородов природного газа.
Прежде чем топливо попадает в батарею ТЭ, оно предварительно очищается от серы, которая отравляет никельсодержащий анод и снижает показатели батареи топливных элементов. Чтобы избежать потерь в работе, уровень серы должен быть ниже 0,1 ppm. Содержание серы в природном газе значительно меньше, чем в жидких нефтепродуктах, но поскольку в него обычно добавляют серосодержащие вещества для придания запаха, то концентрация серы достигает 4...5 ppm. Как правило, для ее удаления используесят каталитический реактор, в котором сера соединяется с водородом в H2S и адсорбируется при повышенной температуре (450 °С) в реакторе [2].
Тяжелые углеводороды в топливе должны быть полностью преобразованы в СО и водород, чтобы избежать образования углерода на топливных элементах. Обычно используется паровая конверсия. Рециркуляция части отработавшего потока может использоваться для обеспечения паром реформера, позволяя повысить долю утилизации топлива, что также является дополнительным преимуществом.
Вследствие скачка напряжения, обусловленного снижением концентрации топлива в направлении выхлопной части элемента, только определенный процент топлива может быть электрохимически преобразован в электрическую и тепловую энергию. Общая утилизация 85…90% рассматривается как практический максимум – при более высоком уровне может окислиться никель. Оставшееся топливо со стороны анода смешивается с избыточным воздухом (с катода) и каталитически сжигается.
Выхлопные газы проводятся через рекуператор для подогрева воздуха, идущего в ТЭ. Температура воздуха на входе элемента должна быть как минимум 500 °С, чтобы избежать термических ударов, которые могут вызвать необратимые повреждения ТЭ. Добавочный теплообменник используется для производства горячей воды. Расположив его между двумя рекуператорами, вместо горячей воды можно получать пар.
Батарея топливных элементов производит постоянный ток. Для его преобразования используется инвертор, КПД которого составляет обычно 94…98% [2]. Кроме того, в состав электрохимических установок входят следующие дополнительные системы:
• вентилятор для подачи воздуха в ЭУ (единственный источник шума и потребитель электроэнергии собственных нужд);
• воздушные фильтры (достаточно простых фильтров);
• нагреватель воздуха для пуска модуля ТОТЭ (иногда используется при низких нагрузках);
• средства управления и устройство связи для дистанционного управления, управления реактивной мощностью;
• система продувки газов (для предотвращения повреждений модуля во время пусков и очистки модуля при аварийном отключении);
• пусковой генератор пара для обеспечения паром реформера.
Электрический КПД электрохимических установок на основе ТОТЭ составляет 45…50% [2] (в расчете на низшую теплоту сгорания топлива), возможно его дальнейшее повышение. Коэффициент использования теплоты топлива достигает 85…90% [2].
Значительно преуспела в производстве электрохимических установок в последнее время фирма Fuel Cell Energy (США). Основное направление ее деятельности – топливные элементы на основе расплавленного карбонатного электролита. Сегодня компания предлагает три модификации установок – DFC-300A, DFC-1500 и DFC-3000 (DFC-direct fuel cell) мощностью 250, 1000 и 2000 кВт соответственно. Подобными установками занимаются также компании MTU (Германия), GenCell (США), Ansaldo (Италия), IHI (Япония) и др. [4].
В области твердооксидных элементов наибольших результатов добились Siemens-Westinghouse (Германия и США) – установки 100 и 250 кВт; Mitsubishi и Chubu Electric Power (Япония); Rolls-Royce (Великобритания) [4].
Применение топливных элементов
В настоящее время топливные элементы, в силу пока еще их небольшой единичной мощности, предполагается использовать в малой энергетике, поэтому конкуренция с мощными парогазовыми установками в ближайшем будущем маловероятна.
Следует рассматривать их перспективу для сегмента рынка от 1 кВт до нескольких мегаватт – здесь они имеют значительные преимущества.
В настоящее время стоимость электрохимических установкок довольно высокая. Например, ориентировочная стоимость электростанций компании Fuel Cell Energy составляет $4500 за кВт установленной мощности [6]. Это является основным препятствием для вывода топливных элементов на широкий рынок. Сегодня значительные средства и силы направлены на снижение затрат на производство топливных элементов. Цель разработчиков – достичь удельной стоимости ниже $1000/кВт.
Несмотря на высокую стоимость ЭУ, потребители находятся уже сейчас – это отели, университеты, больницы, водоочистительные станции, телекоммуникационные центры, коммерческие и промышленные объекты. В недалеком будущем электрохимические установки могут широко использоваться для децентрализованного и автономного энергоснабжения отдаленных поселков и небольших городов, промышленных и сельскохозяйственных предприятий, нефтяных платформ и газотранспортных магистралей. 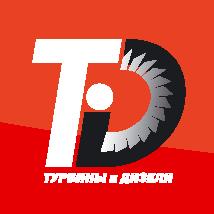
Использованные источники
1. Коровин И. В. Топливные элементы и электрохимические энергоустановки. М.: издательство МЭИ, 2005. – 280 с.
2. Edited by S.C. Singhal, К. Kendall. High-temperature solid oxide fuel cell: fundamentals, design and applications. Imprint: Elsevier advanced technology. 2003. – 405 p.
3. Opening doors to fuel cell commercialization. Fuel reforming, (www.fuelcelltoday.com)
4. Fuel cell today Market Survey: large stationary applications. 2 November 2005. (www.fuelcelltoday.com Johnson Matthey).
5. Website: www.powergeneration.Siemens.com. (фирма Siemens AG)
6. Website: www.fce.com (фирма Fuelcell Energy).