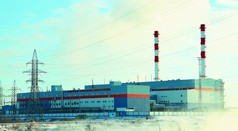
Total electric output of the station is 122.6 MW, thermal output is 110 MW. The main fuel for the station is cross-country pipeline natural gas. The station consists of two combined cycle power units on the base of GE Energy MS6001B gas tubines each rated at 42 MW. P-131 heat recovery steam generators were supplied ZIOMAR engineering company. Two Ò-15.5/20.3-5.4/0.2 steam turbines were manufactured and delivered by Kaluga Turbine Plant, electric generators for steam turbines were supplied by Electrotyazhmash-Privod.
Construction was performed by the Intertechelectro-New Generation group of companies. The Noyabrsk CCGT power plant is the first large centralized power source and the only generation facility in the Yamal-Nenets autonomous district having such performance. It was fully constructed on the basis of private investments and this is the first medium-power facility built by an independent investor after the Russian Federation power industry reform.
The power plant constitutes the first stage of implementation of the «Industrial Urals-Polar Urals» Project power unit. This power plant is an entity of wholesale electricity market and is included into the summary forecasted balance of electric power generation and supply within the framework of UES of Russia.